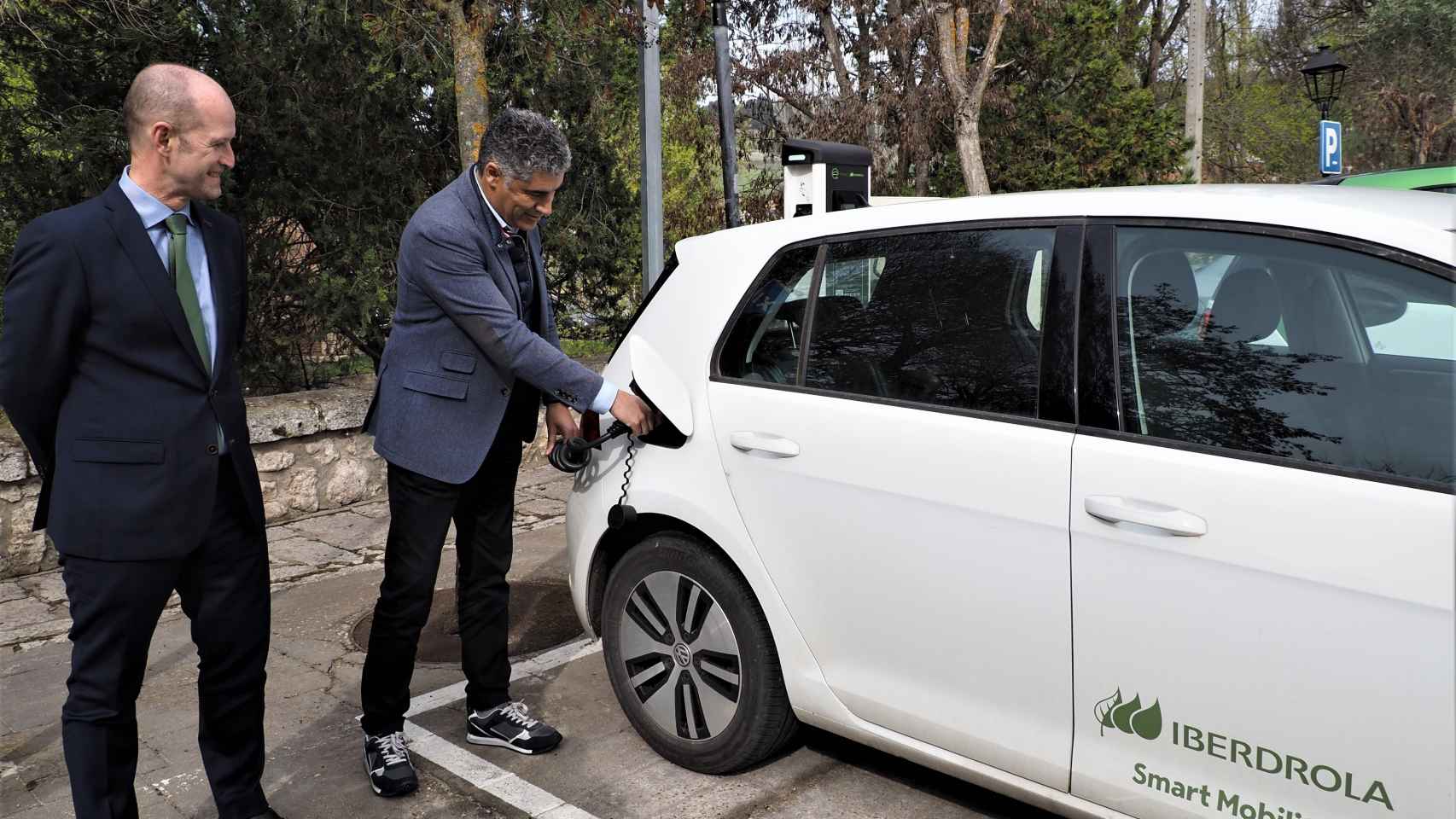
Una instalación de nuevos puntos de recarga para el vehículo eléctrico.
El País Vasco recurre a la sal de cesio para aumentar la vida útil de las baterías del futuro vehículo eléctrico
Investigadores de la Universidad del País Vasco dan con una fórmula disruptiva que se suma a otras como las presentada en Valencia.
16 abril, 2022 04:27Noticias relacionadas
- Una antigua fábrica de tornillos reconvertida en epicentro del futuro talento de la industria 4.0 de Bilbao
- La innovación valenciana se tiñe de 'verde' con coches eléctricos más eficientes y probióticos de cerveza
- Industria vasca y energía: viaje al centro de la innovación aplicada a proyectos de almacenamiento
Mucho se ha hablado de la ejecución en Sagunto (Comunidad Valenciana) de la esperada gigafactoría de baterías del grupo Volkswagen. Se trata, como se ha insistido, de un proyecto clave relacionado con el vehículo eléctrico del futuro, pero eso no significa que éste sea el único proyecto clave.
Y es que, de manera paralela al anuncio de este tipo de macroplanes, hay un trabajo en la sombra encaminado a dar valor a las baterías que se producen en esas fábricas.
Hablamos de los equipos de investigación que trabajan por conseguir que esas baterías sean más eficientes. Y, cómo no, la ciencia, la innovación y la tecnología tienen mucho que decir.
Uno de los últimos proyectos que se ha conocido en este sentido, proviene de la iniciativa pública del País Vasco. En concreto, se trata de una investigación de un equipo multidisciplinar de químicos y físicos de la Universidad del País Vasco (UPV/EHU) en colaboración con el centro tecnológico CIC energiGUNE.
Este grupo ha demostrado que añadiendo una sal de cesio en el electrolito de las baterías de sodio-aire (Na-O2) aumenta notablemente la vida del dispositivo lo que impactaría positivamente en la autonomía del vehículo eléctrico. El trabajo ha sido publicado en la prestigiosa revista internacional 'Advanced Energy Materials'.
Las baterías de metal-aire son una tecnología prometedora para suceder a las actuales baterías de iones de litio convencionales. Entre las ventajas que cuentan las baterías de metal-aire la más significativa reside en contar con una mayor densidad de energía que las de iones de litio, por lo que este tipo de baterías ofrecería al automóvil una mayor autonomía.
Gracias a ellas, una de las grandes preocupaciones de los fabricantes de automóviles, como la autonomía, conseguiría minimizarse de una forma considerable, explican desde la UPV/EHU.
"Las baterías de metal-aire se encuentran entre las más sostenibles ya que los materiales que se utilizan son más respetuosos con el medio ambiente. Estas baterías toman oxígeno del aire, realizan sus procesos electroquímicos para generar la electricidad y cuando hay que volver a cargar la batería vuelven a emitir el oxígeno; es decir, funcionan consumiendo oxígeno y liberando oxígeno. Por eso, se conocen también como las baterías que respiran", comenta Idoia Ruiz de Larramendi investigadora del departamento de Química Orgánica e Inorgánica de la Facultad de Ciencia y Tecnología de la UPV/EHU.
Sin embargo, "no todo son ventajas. Uno de los problemas asociados a estas baterías es que presentan una pobre ciclabilidad, es decir, hacen pocos ciclos de carga y descarga", dice Ruiz de Larramendi.
Así es la investigación
Por ello, "en este trabajo de investigación nos hemos centrado en el diseño racional de electrolitos para su implementación en baterías de sodio-aire. En la actualidad, la mayoría de las baterías del mercado son de iones de litio. Sin embargo, el litio es un metal de abundancia limitada restringida en sólo unos pocos países por lo que en los últimos años se ha despertado el interés en el desarrollo de baterías basadas en sodio como alternativa, ya que se trata de un elemento más abundante, barato y sostenible", señala la investigadora de la UPV/EHU.
El electrolito es el encargado de dar movilidad a los iones dentro de la batería. "Nuestro objetivo ha sido conseguir que esa movilidad sea la óptima. Para ello, en este estudio hemos trabajado con dos aditivos: el tetrabutilamonio (TBA) y el cesio (Cs) y hemos evaluado el potencial que presentan para mover los aniones de oxígeno por la batería", resume.
"Aplicando los principios de la química y apoyándonos en estudios teóricos entendíamos que se iban a unir mejor a los aniones de oxígeno, y así ha sido en ambos casos", añade Idoia Ruiz de Larramendi.
"Sin embargo —continúa—, los cationes de cesio han demostrado tener mayor potencial y ser más eficaces que los cationes de TBA porque la carga del Cs es más accesible para el oxígeno. Al añadir una sal de cesio hemos conseguido mejorar la ciclabilidad y llegar hasta más de 90 ciclos de carga y descarga. A día de hoy, puede parecer que es poco, pero supone un gran avance hacia la futura comercialización de estos dispositivos".
Según el equipo multidisciplinar, "obviamente, es mejorable y tenemos que seguir trabajando en ello, pero este trabajo es un importante paso en el que se demuestra que con una estrategia tan sencilla como la de añadir una sal de cesio en el electrolito, mejoramos notablemente su número de ciclos, lo que nos permite soñar con una nueva generación de vehículos eléctricos de mayor autonomía", concluye.
Cabe recordar, tal y como avanzó D+I a principios de este año, que otras iniciativas público-privadas españolas estaban trabajando en la misma línea de mejorar la durabilidad de las baterías.
El proyecto valenciano
Precisamente en la Comunidad Valenciana -región que albergará la anhelada gigafactoría de baterías-, se ha desarrollado un proyecto respaldado por la agencia pública de innovación (AVI).
Su objetivo es sustituir las piezas metálicas de estos dispositivos por resinas sintéticas -conocidas como composites- con propiedades mejoradas, con el fin de aligerarlos entre un 50% y un 70%.
El proyecto Lightcar, que lidera Industrias Alegre, y en el que participan las empresas Itera, Sinfiny Smart Technologies y el Instituto Tecnológico del Plástico (Aimplas), ayudará a la industria de la automoción a completar la transición hacia una movilidad más sostenible gracias al diseño de una nueva generación de vehículos eléctricos más eficientes.
Para alcanzar este objetivo, la reducción del peso se erige en un factor determinante, ya que un coche más ligero requiere menos energía para ser impulsado. Es decir, con las mismas baterías la autonomía aumenta considerablemente respecto a automóviles más pesados.
Construidos sobre una estructura de aluminio y acero inoxidable, los acumuladores de energía actuales representan, de hecho, entre el 20% y el 30% del peso total de estos vehículos. Por este motivo la industria de automoción está comenzando a sustituir estas piezas por materiales compuestos que permiten reducir su peso hasta un 70%.
Por eso este proyecto apuesta por el desarrollo de composites termoplásticos de fibra larga que destacan por su ligereza, rigidez y resistencia a impactos y que, a diferencia de otros productos en el mercado, se pueden reciclar y procesar mediante métodos convencionales de fabricación, también eficientes y con una baja generación de residuos.