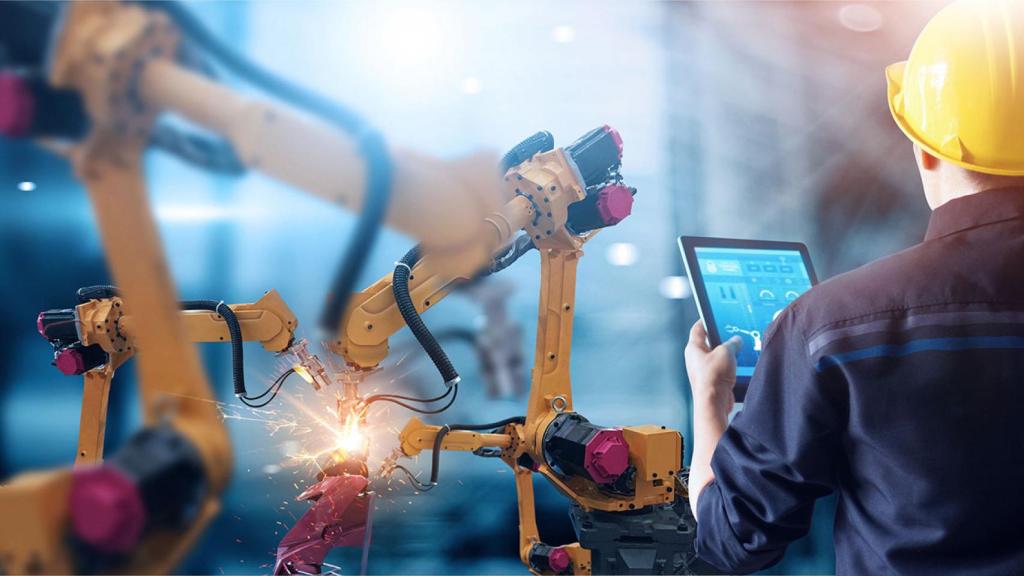
Planta de producción digitalizada.
La fábrica del futuro: cuando las cadenas de montaje dejan lugar al análisis de datos
El Instituto Tecnológico de Informática (ITI) trabaja en un proyecto que mejore la adquisición y explotación de los datos en el entorno industrial.
4 septiembre, 2021 02:44Noticias relacionadas
- Industria 4.0 para ‘simplificar, automatizar y optimizar las cadenas de producción con datos en tiempo real’
- Innovación española para dar el salto hacia la industria 4.0 en el sector aeronáutico
- Bind 4.0 brinda las ideas más disruptivas en Industria 4.0, energía 'verde', 'ehealth' y 'foodtech' a 65 empresas
El desarrollo de la industria 4.0 es imparable y no está exenta de retos no siempre fáciles de resolver. Uno de los más importantes es la correcta captación y uso de los datos, la materia prima en la digitalización de cualquier sector.
Para obtener los mejores resultados posibles, es fundamental obtener esos datos de manera automatizada, en tiempo real y cumpliendo unos mínimos estándares de calidad. Y en ello está trabajando el Instituto Tecnológico de Informática (ITI) desde hace un año.
“Cuando hablamos con empresas [que han iniciado su digitalización] encontramos problemas recurrentes como los conocidos silos de datos o la escasa integración”, explica Jordi Arjona, coordinador del grupo de Sistemas Distribuidos (SiDi) de ITI.
“Para resolverlos, es necesario trabajar en la unificación de los distintos orígenes de datos de los que disponen las compañías y mejorar las conexiones y flujos de datos intra e interempresa” añade.
HyperFactory es un proyecto encaminado al desarrollo de una arquitectura multinivel orientada al dato, a su adquisición, gestión y explotación en un entorno industrial.
Integración del dato
Uno de los objetivos de HyperFactory es “avanzar hacia la factoría hiperconectada”, apunta Arjona. Para conseguirlo, el equipo de ITI ha abordado cada uno de los ámbitos donde se generan y se utilizan estos datos, estos son líneas de producción, planta y dirección de la empresa.
Para el desarrollo del programa han realizado un paralelismo entre la industria y los niveles con los que se trabaja hoy en día en computación. “En el proyecto se iguala la dirección de la empresa a una capa cloud, la factoría a la capa fog y las distintas líneas de producción a la capa edge”, describe el investigador.
Esta estrategia persigue distintos objetivos. “Con respecto al edge, se trata de buscar mecanismos que hagan más eficiente y resiliente la comunicación de datos dentro de la fábrica. En fog, constituir un repositorio de datos que agregue la información no sólo proveniente de las líneas de producción –independientemente de los distintos protocolos con que trabajen–, sino que también permita integrar de manera sencilla información de negocio o comercial”, describe Arjona.
“Finalmente, el nivel cloud tiene a su alcance los medios para recuperar y contextualizar aquella información que requiera, ganando una mayor visibilidad de lo que sucede en la empresa y aumentando su capacidad de acción”. El resultado permitirá generar una arquitectura flexible y dinámica, pero robusta y segura a la vez.
HyperFactory, aseguran desde ITI, permitirá incrementar la eficiencia y capacidad de adquisición, gestión y procesado de datos de la planta digitalizada; así como su explotación para obtener nuevas herramientas para la mejora de procesos productivos y de negocio; junto a la disponibilidad de un soporte compartido entre los actores involucrados, como empresas o fabricantes de maquinaria, que mejore la integración de los datos para una adecuada digitalización de la industria.
El proyecto, que ya dispone del diseño tanto de la arquitectura como de los componentes que pretenden dar respuesta a las necesidades de la fábrica, cuenta con el apoyo del Instituto Valenciano de Competitividad Empresarial (IVACE) y el Fondo Europeo de Desarrollo Regional (FEDER).