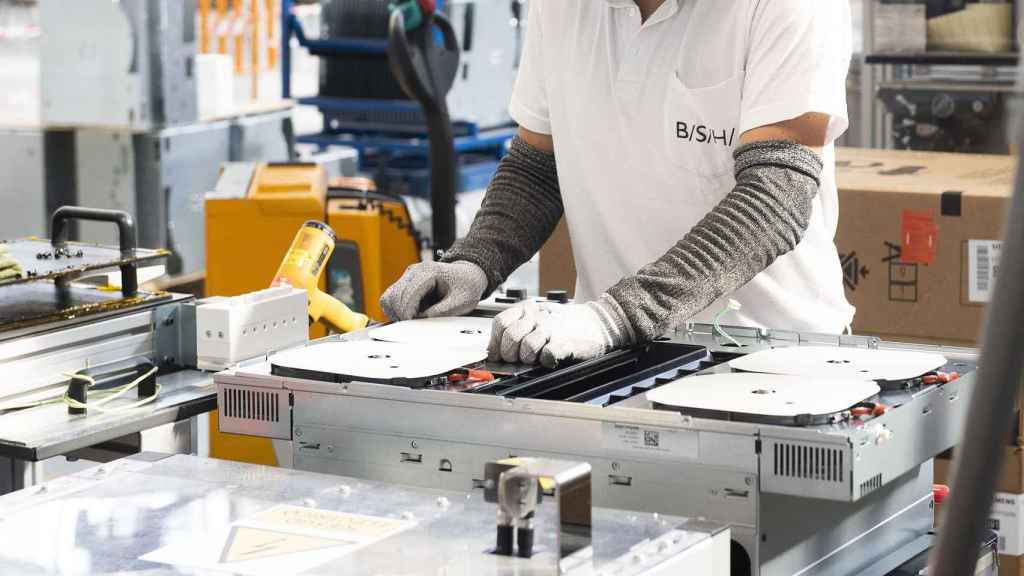
Montaje de placas en las instalaciones de BHS Electrodomésticos en España.
Dentro del centro español de I+D que desarrolla y fabrica uno de los electrodomésticos icónicos de la alemana BSH
DISRUPTORES - EL ESPAÑOL visita las antiguas instalaciones de Balay en Zaragoza, ahora parte de BSH, donde diseñan la electrónica y el software, y producen las placas de inducción de todas las marcas del grupo.
8 junio, 2024 01:54La cotidiano está lleno de innovación y mucha de ella salida de nuestro país. Uno de los ejemplos más recurrentes es la fregona. Un artículo inventado por el militar riojano Manuel Jalón en los años 50, que no solo facilitó la limpieza en los hogares, sino que también acabó con algo con tedioso como fregar de rodillas, restregando el suelo a mano con una bayeta y arrastrando un cubo con agua.
Las labores del hogar siempre han sido objeto de estudio para mejorar la vida de las personas. Atrás quedaron los días en los que se lavaba la ropa a la orilla del río frotándola contra una tabla o se cocinaba a la lumbre gracias a los desarrollos tecnológicos. Algo de lo que saben, y mucho, en los nueve centros de innovación que tiene en España la alemana BSH, fabricante de electrodomésticos de marcas como Bosch, Siemens, Balay, Neff o Gaggenau.
En esos nueve centros trabajan alrededor de 350 investigadores que desarrollan soluciones para todos los mercados en los que la compañía está presente. El más emblemático es el que está en Zaragoza, a solo 15 minutos en coche de la estación del AVE y localizado en las instalaciones que pertenecieron a la española Balay, hasta que en 1989 se integró en BSH.
Aquí, además de estar los laboratorios donde diseñan la tecnología que está detrás de las placas de inducción de todo el grupo, también se ubica la planta manufacturera donde las producen y distribuyen por todo el mundo. Su volumen de trabajo es tal, que cada 15 segundos se fabrica una placa y cada 20 segundos un horno, la otra de sus líneas de producción.
El hecho de que sea en el barrio zaragozano de Montañana donde se concentre el desarrollo y fabricación de este electrodoméstico no es casual. “A finales de los años 80, decidimos explorar la posibilidad de calentar recipientes domésticos mediante inducción. Así, en colaboración con la Universidad de Zaragoza, lanzamos nuestro primer producto exclusivo para la marca Balay”, explica José Andrés García, director del Centro de Desarrollo de placas eléctricas del Grupo BSH, durante una visita de DISRUPTORES – EL ESPAÑOL a las instalaciones.
El desafío del hardware
Desde entonces, y a lo largo de todos estos años, han pasado de producir entre 15.000 y 20.000 unidades anuales a rondar los 1,5 millones, adaptándose a las necesidades del mercado y a las posibilidades técnicas. “Al principio, la tecnología existente no permitía integrar la electrónica directamente en las placas porque no soportaba las altas temperaturas a las que había que someterla”, recuerda García.
No fue hasta 1999 cuando consiguieron integrar esa electrónica, “logrando un hito significativo y eliminando la necesidad de una caja externa”. “Esto permitió que las placas se instalaran sobre los hornos, optimizando el espacio en la cocina y mejorando la experiencia del usuario”, describe el directivo.
"A finales de los años 80, ya exploramos junto a la Universidad de Zaragoza la posibilidad de calentar recipientes domésticos mediante inducción"
En 2003, lanzaron una nueva generación con zonas de cocción dedicadas al pescado para le mercado alemán y más adelante para la paella en el mercado español. En 2010 introdujeron la ‘zona Flex’, permitiendo al usuario mover el recipiente por la superficie manteniendo el mismo nivel de potencia y convirtiéndose en pioneros en esta tecnología.
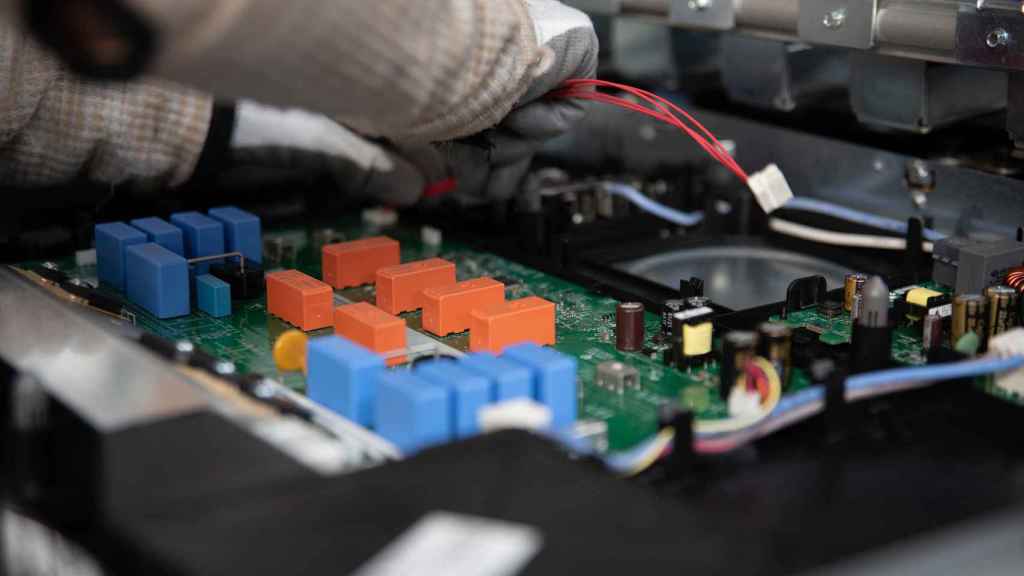
Montaje de la electrónica de una placa de inducción Montañana (Zaragoza).
El proyecto en colaboarción con Cosentino es una buena muestra de ello, un concepto en el que han trabajado durante 10 años y que han ejecutado en los últimos dos antes de ponerlo en el mercado. “Lo más complicado ha sido seleccionar un material que tuviera las propiedades mecánicas y térmicas que precisábamos”, explica el director de I+D.
Finalmente, eligieron una de las propuestas de la empresa española, dedicada a la producción de superficies para arquitectura, el Dekton, por su resistencia y durabilidad, “que permite una superficie de cocción más versátil y resistente, capaz de soportar altas temperaturas y cambios bruscos sin riesgo de rotura”, asegura García.
Desarrollo de software
Toda la parte de la electrónica la llevan desde el departamento denominado ‘Electronics and Drive’ (Electrónica de interfaz de usuario). “Aunque en el nombre se menciona motores, en realidad no trabajamos con ellos. Actualmente, el 80% de nuestras actividades están relacionadas con el software, aunque también nos dedicamos a la verificación y especificaciones”, aclara el jefe de desarrollo de la planta, Ignacio Garde.
Garde cuenta con un equipo de 50 personas en Montaña, formado principalmente por ingenieros superiores con formación en ingeniería informática, telecomunicaciones y sistemas automáticos. Esta área nació en 2016 con seis personas como una spin-off dedicada a la electrónica de inducción. “Con el tiempo, hemos ampliado nuestras capacidades para incluir el desarrollo de software más complejo, como el de las pantallas TFT”.
“Hemos fomentado la innovación para convencer a los responsables alemanes de nuestra capacidad para liderar este mercado desde España"
Un crecimiento que se ha visto impulsado por el aumento de la demanda de servicios electrónicos y software en el sector de los electrodomésticos. Esto llevó a unificar todas las áreas dedicadas a ellos bajo una misma unidad en 2019 que, a su vez, colabora con el resto de centros de desarrollo en Alemania, Eslovaquia y China.
“Nuestro crecimiento también ha sido posible gracias a la colaboración con empresas externas españolas, algunas localizadas en Zaragoza y otras con sede en Málaga, nos han permitido escalar nuestros proyectos y abordar problemas de rendimiento con rapidez y eficacia”, añade el jefe de desarrollo.
"El 80% de nuestras actividades están relacionadas con el software"
En España, este equipo trabaja en tres áreas. Una es la electrónica de potencia para placas de inducción. La segunda está dedicada al Central Computing Module (CCM), una unidad central de computación integrada en todos los nuevos electrodomésticos “Esta unidad actúa como un pequeño ordenador, gestionando tanto la conectividad como la lógica del aparato”. Ahora, están desarrollando la tercera generación en colaboración con equipos en Alemania, dividiendo el trabajo aproximadamente al 50%.
Inteligencia artificial para hornear
La tercera de las áreas está dedicada a la inteligencia artificial, de momento enfocada a la gama de hornos, que tradicionalmente ofrecen múltiples opciones de configuración que pueden resultar abrumadoras para sus usuarios. BSH ha abordado esta complejidad implementando programas preconfigurados que simplifican el proceso.
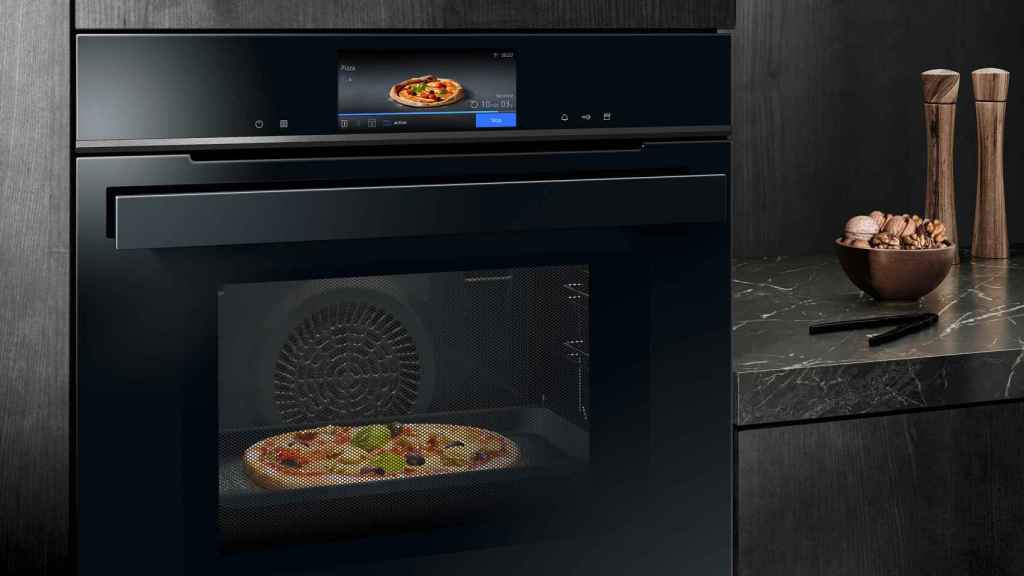
Detalla del horno Siemens iQ700 con inteligencia artificial.
“Por ejemplo, al cocinar una pizza, los sensores pueden detectar el punto de cocción ideal, ajustando automáticamente la temperatura y el tiempo según sea necesario”, explica Ramón Peinado, responsable del equipo de Inteligencia Artificial del Centro de Competencia de Electrónica de BSH España, mientras introduce una pizza en un horno para realizar una demostración en la cocina de su laboratorio.
Para conseguir esto, BSH ha integrado cámaras en sus hornos que imitan la percepción humana, permitiendo que "vea" los alimentos y determine cuándo están listos. “Esta tecnología de visión por computadora permite al horno tomar decisiones basadas en la apariencia del alimento, como el color y el nivel de tostado, asegurando resultados óptimos”, asegura Peinado.
Este sistema cuenta con una capacidad de aprendizaje continuo que permite que se actualice regularmente con nuevos programas y ajustes, adaptándose a las necesidades de los usuarios. “Este modelo empezó a venderse sin capacidades de IA, pero gracias a las actualizaciones de software, los usuarios han podido beneficiarse de esta nueva funcionalidad”, ejemplifica el responsable de IA.
Producción global desde Zaragoza
La implantación de tecnología en la filial de BSH en España también abarca procesos de oficina, documentación y optimización del flujo de trabajo. Además, dentro de la fábrica, ya están llevando a cabo un proyecto piloto que busca integrar completamente la digitalización en su línea de ensamblaje, incluyendo la colocación de componentes electrónicos, el pegado de cristales y perfiles, la aplicación de silicona conductora, y medidas de seguridad para garantizar la resistencia de los productos.
“Uno de los próximos proyectos que vamos a lanzar se centra en el suministro autónomo. Por ejemplo, tenemos un sistema de transporte automatizado que se asemeja a un robot tipo "Roomba". Este robot puede ser programado para entregar productos de un punto a otro de manera autónoma, evitando obstáculos en su camino”, describe Juan Luis Cihuelo, coordinador de actividades Industria 4.0 en la planta de BSH en Montañana, durante la visita a la zona manufacturera. Actualmente, están construyendo un tren con seis vagones que se moverá entre puntos específicos, suministrando material a diferentes líneas de producción.
"Antes de construir una nueva línea, la simulamos en un entorno virtual para identificar problemas potenciales y realizar ajustes”
En la fábrica, también cuentan con un laboratorio donde emplean la realidad virtual para optimizar sus procesos de producción. “Antes de construir físicamente una nueva línea, la simulamos en un entorno virtual, lo que nos permite identificar problemas potenciales, realizar ajustes y garantizar una implementación más eficiente en el mundo real”, explica Cihuelo. “Esta tecnología nos proporciona una visión detallada de cómo funcionará la línea de producción antes de invertir recursos, lo que nos ayuda a minimizar errores y maximizar la eficiencia desde el principio”.
La ergonomía de los empleados también es un aspecto que están tratando de mejorar. Para ello, utilizan trajes equipados con sensores para registrar los movimientos de los empleados mientras realizan tareas específicas. “Estos datos nos permiten evaluar la ergonomía de cada puesto de trabajo y hacer los ajustes necesarios para garantizar la seguridad y comodidad de nuestros trabajadores”, describe el responsable del laboratorio. Para cerciorarse de que los resultados son los correctos, llevan a cabo pruebas en el mundo real para validar los diseños y asegurarse de que cumplen con los estándares.
Y todo esto desde un barrio de Zaragoza, donde este grupo alemán, que en 2023 facturó 14.890 millones de euros (de los que el 5,7% destinan a I+D), desarrolla y produce de principio a fin las placas de inducción que sus marcas comercializan por todo el mundo. En España, según los últimos datos proporcionados por la compañía, los ingresos en 2022 se elevaron hasta 1.715,7 millones de euros, logrando un crecimiento del 9,9% respecto al ejercicio anterior.
Detrás de esa cifra, hay 4.000 empleados, de los 60.000 totales con los que cuenta BSH en todo el mundo. De ellos, en las instalaciones de Montañana contabilizan cerca de 250 investigadores y algo más de 900 personal en fábrica. Todos trabajando por llevar la innovación española a los hogares de cualquier parte del mundo.