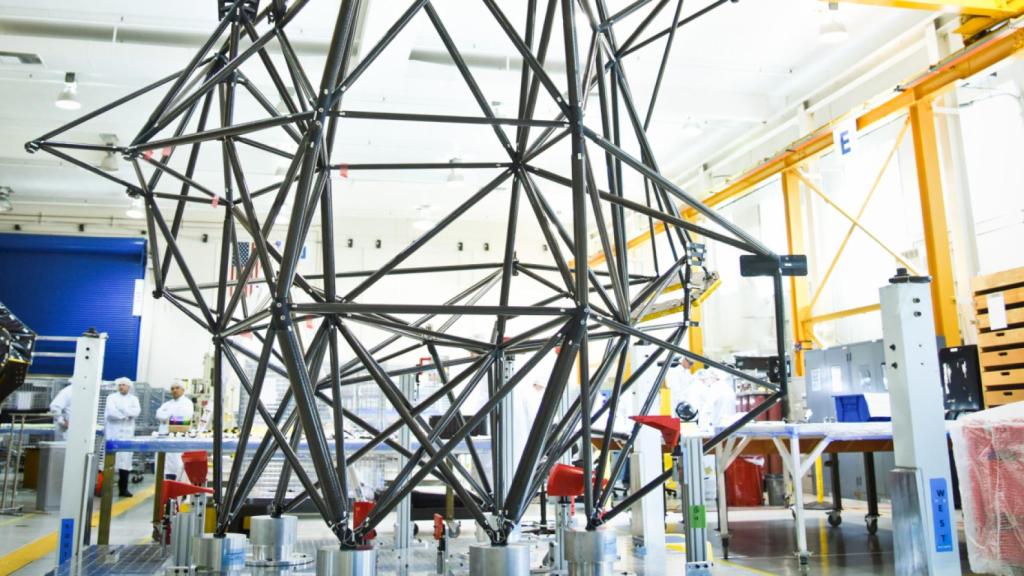
Torre de la antena satelital que ha sido fabricada mediante impresión 3D.
Satélites ligeros y más sostenibles gracias a la impresión 3D
Hispasat pone en órbita su primera torre de antena obtenida con fabricación aditiva: pesa menos, es más precisa y reduce costesrn
21 junio, 2018 07:00Desde elementos para la industria de la automoción a chips de toda clase pasando por juguetes o textiles. La impresión 3D es cada vez una realidad más extendida en todo tipo de sectores y el espacial no se queda atrás. El operador de satélites español Hispasat ha decidido emplear también las ventajas que ofrece la fabricación aditiva enviando al espacio uno de los primeros satélites de telecomunicaciones formado, en parte, por componentes impresos mediante esta tecnología.
El Hipasat 30W-6, el último que el operador español ha puesto en órbita, cuenta con una torre de antena construida mediante fabricación aditiva. El estado del arte de esta tecnología ha sido la principal barrera para que su introducción se haya dilatado en el tiempo. Los requisitos de calificación de cualquier tecnología para su uso en vuelo son muy estrictos y la impresión 3D no es una excepción. «El momento es ahora porque la tecnología está madurando mucho en dos elementos: los acabados y las terminaciones», explica Antonio Abad, director técnico y de operaciones de Hispasat, garantizando así la alta precisión que exige esta industria.
En el caso español su uso no fue premeditado, sino que se decidió acudir a este sistema de fabricación para resolver un problema: durante el desarrollo del satélite su peso superó lo estimado y había que buscar una salida para reducir el crecimiento de la masa. «Cuando lanzamos un satélite tenemos una masa máxima que nos fija el lanzador. Ésta está compuesta por la mesa seca (la estructura y el equipamiento) y la de combustible», dice Abad. Generalmente, la forma de reducir ese peso asignado es disminuir la cantidad de combustible que porta el satélite. ¿El problema? Que eso reduce su vida útil y encarece su uso. Y ahí surgió la impresión 3D como solución.
El resultado: han logrado reducir la masa casi a la mitad, manteniendo la integridad estructural. Y así, mientras la vida útil media de estos satélites es de 15 años, en el caso del 30W-6 aseguran que será superior ya que dispone de más combustible y menos peso con el que trabajar.
La principal diferencia, en comparación con la fabricación tradicional, es que se ha podido eliminar el mecanizado de piezas necesario para liminar material y obtener la geometría particular que se requiere para este tipo de operaciones. Y se ha sustituido por un proceso de adición de capas de material, que es más rápido, más económico y más sostenible, ya que la cantidad de material desechado se reduce considerablemente. Con este proceso se ha disminuido la complejidad en la construcción, ya que se ha podido combinar varias piezas en una sola, y se ha acelerado el proceso.
Estas torres se habían fabricado tradicionalmente con paneles sólidos que conformaban una estructura continua, pero ahora se trabaja con nuevos diseños a base de tubos huecos que pesan mucho menos. Space Systems Loral es la compañía fabricante de este satélite y lanzó la primera de estas torres a finales de 2016. La del satélite de Hispasat es tres veces mayor que aquella, contiene más de 200 barras de fibra de carbono y es la estructura de soporte de antenas más grande y compleja que la compañía ha desarrollado hasta la fecha con este tecnología.
Sin embargo, en la actualidad solo se está aprovechando un pequeña parte (aunque importante) de todo lo que la fabricación aditiva puede hacer por la industria aeroespacial. «Estamos en la primera etapa: sustituir algunas piezas por impresiones en 3D. La segunda vendrá cuando el diseño se haga directamente pensando en esta tecnología», asegura Abad, porque ahora se trabaja con planos y esbozos clásicos que finalmente se migran al universo de la fabricación aditiva. «Si empezamos a diseñar sin las restricciones de las tecnologías de construcción clásicas, daremos lugar a nueva generación de diseño que ni siquiera podemos imaginar».
Con esa previsión en mente, el futuro es prometedor. «No solo pensamos en repetir, sino en aumentar el número de elementos fabricados en 3D en próximos satélites. Las ventajas son muy atractivas por la reducción de masa y la facilidad de fabricación», explica el responsable de Hispasat. Y todo ello se traduce en una reducción de costes tanto para la compañía como para los clientes que finalmente pagan por sus servicios.
rn