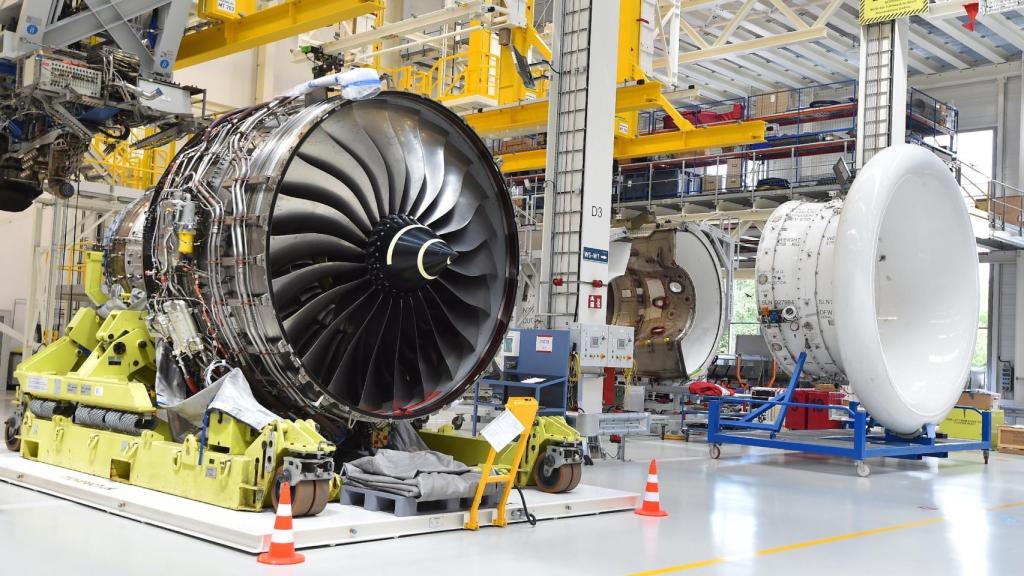
Un motor a reacción Rolls-Royce en una planta de fabricación en Alemania Omicrono
El material que revolucionará los aviones y la exploración espacial: aleaciones de titanio más resistentes y flexibles
Un equipo de investigadores del MIT han descubierto la mejor combinación de materiales para abrir nuevos caminos en el sector aeroespacial.
19 julio, 2024 02:26La ciencia de los materiales está detrás de muchos de los avances que llegan a nuestro día a día. Las investigaciones en torno a la relación entre su estructura y sus propiedades tienen especial relevancia en sectores como el de defensa, el aeronáutico o el aeroespacial, siempre a la búsqueda de nuevas soluciones. Además de recientes avances como la llegada de los primeros aviones eléctricos de pasajeros y motores como el de la española Pangea Aerospace, destinado a revolucionar la exploración espacial, los esfuerzos se centran en conseguir materiales que desafíen los límites actuales y ofrezcan oportunidades todavía inexploradas.
En eso llevan trabajando desde hace años varios investigadores del Instituto de Tecnología de Massachusetts (MIT), junto con ingenieros de la empresa estadounidense ATI Specialty Materials, con amplia experiencia en la producción de todo tipo de metales en aeronaves y plataformas militares. De forma conjunta, este equipo ha descubierto un método para obtener nuevas aleaciones de titanio "con una combinación excepcional de resistencia y ductilidad", que pueden ser clave para mejorar las prestaciones de grandes turbinas, componentes de aviones y hasta cohetes espaciales.
En un estudio publicado en la revista Advanced Materials, los responsables de la investigación describen cómo han desarrollado nuevas técnicas, como la del laminado cruzado, y han modificado las proporciones de los elementos para conformar aleaciones de titanio más resistentes, flexibles y duraderas que las existentes hasta la fecha.
Aleaciones de titanio
Las aleaciones de titanio se obtienen mezclando este metal con otros elementos químicos, como el aluminio o el oxígeno, y se llevan utilizando desde principios del siglo XX con distintas funciones y objetivos. Su principal atractivo reside en su resistencia a la tracción y a la corrosión y a su extremada ligereza, pero también en su capacidad para soportar temperaturas extremas. Eso las hace ideales para su uso en infraestructuras aeroespaciales como la ISS, por ejemplo, pero también para fabricar componentes de automóviles, prótesis médicas y hasta pequeñas herramientas para llevar siempre encima o anillos para monitorizar tu salud.
A la hora de diseñar y desarrollar las aleaciones hay dos características clave que no siempre son fáciles de equilibrar: resistencia y ductilidad. Y es que el titanio más fuerte suele ser menos deformable, y el más dúctil tiene a ser mecánicamente más débil. El equipo del MIT ha trabajado precisamente en lograr las mejores combinaciones posibles, adaptando la composición química y la estructura reticular de cada aleación y utilizando técnicas de procesamiento únicas que permitirán producir los materiales a escala industrial.
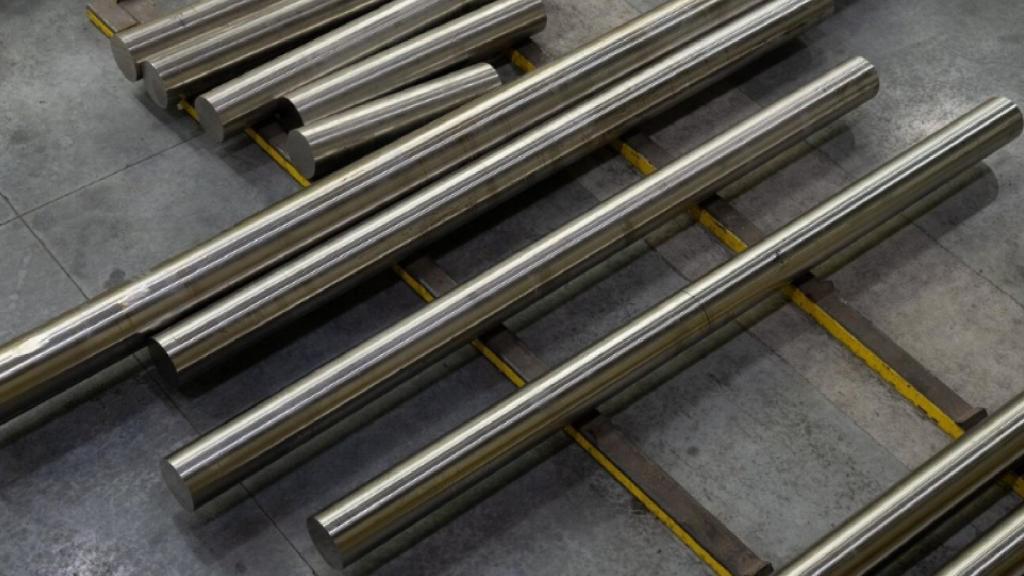
Barras de aleación de titanio Omicrono
Su misión, encontrar la fórmula más precisa entre los elementos de la aleación y sus proporciones y cambiando la manera en que se procesa el material, pasó por "crear un gran campo de juego para obtener buenas combinaciones de propiedades, tanto para temperaturas criogénicas como elevadas", afirma Cemal Cem Tasan, coautor del artículo y catedrático de Ciencia e Ingeniería de Materiales del MIT en un comunicado de prensa.
Para lograrlo hay que estudiar la escala atómica, donde se observan las dos fases de las aleaciones de titanio, conocidas como alfa y beta. "La estrategia clave en este enfoque de diseño es tener en cuenta diferentes escalas", señala Tasan. "Una escala es la estructura del cristal individual. Por ejemplo, eligiendo cuidadosamente los elementos de aleación, se puede tener una estructura cristalina de la fase alfa que permita mecanismos de deformación particulares. La otra escala es la del policristal, que implica interacciones de las fases alfa y beta. Así que el enfoque que se sigue aquí implica consideraciones de diseño para ambas".
La mejor combinación
En su investigación en el laboratorio, en la que también participaron los ingenieros de ATI, estos expertos en metalurgia analizaron con detalle multitud de aleaciones a través de un microscopio electrónico de barrido. Así descubrieron, deformando los materiales para conocer cómo respondían sus microestructuras a la carga mecánica externa, que la técnica de laminado cruzado era fundamental para lograr las mejores combinaciones de resistencia y ductilidad.
En colaboración con el Centro de Sistemas a Nanoescala de la Universidad de Harvard, los investigadores dieron con la combinación de parámetros que ofrecía el mejor resultado, en el que las fases alfa y beta compartían la deformación de manera uniforme. Eso implicaba reducir drásticamente la tendencia a la aparición de grietas, habitual cuando las fases responden de manera diferente ante el estrés mecánico.
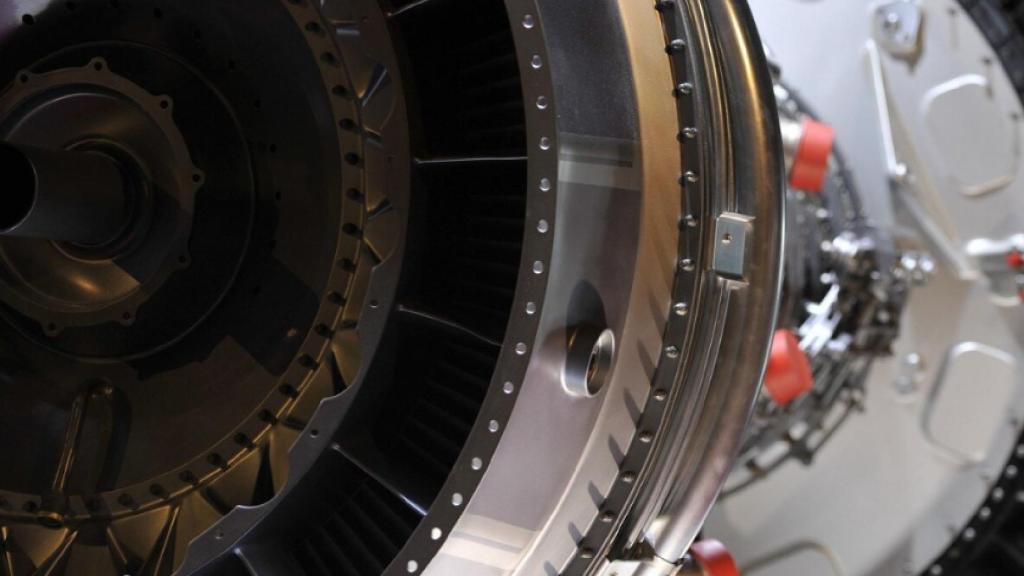
Uno de los motores con aleación de titanio de ATI Specialty Materials Omicrono
"Estudiamos la estructura del material para comprender estas dos fases y sus morfologías, y examinamos sus químicas realizando análisis locales a escala atómica. Adoptamos una amplia variedad de técnicas para cuantificar diversas propiedades del material a través de múltiples escalas de longitud", asegura Tasan. Contrastados los resultados, concluyeron que las propiedades obtenidas eran "mucho mejores que las de aleaciones comparables".
Esta investigación, que ha supuesto la validación científica de la estrategia de diseño y de su producción a escala, proseguirá ahora su camino con el apoyo de la industria para llegar a la comercialización de las aleaciones más prometedoras. Su potencial es el de marcar un antes y un después en la fabricación de componentes de motores de todo tipo de vehículos, sistemas de escape en aviones y estructuras de satélites más ligeras y resistentes a temperaturas extremas. El propio Casan habla de las nuevas oportunidades que ofrece para "cualquier aplicación aeroespacial en la que sea útil una combinación mejorada de resistencia y ductilidad".