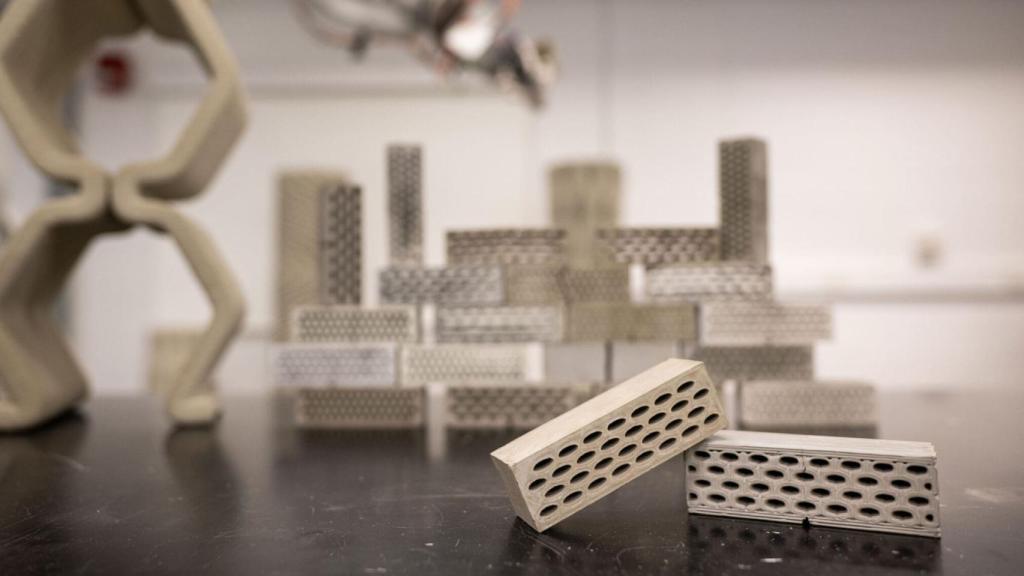
Los ladrillos de cemento desarrollados por investigadores de Princeton Omicrono
Este hormigón quiere cambiar la construcción: es 5,6 veces más resistente gracias a imitar a los huesos humanos
Ingenieros de la Universidad de Princeton han desarrollado una pasta de cemento con mayor tenacidad frente a las grietas gracias al fémur humano.
23 septiembre, 2024 01:39Aún no sabemos cómo serán los edificios del futuro en España, pero teniendo en cuenta todos los avances en los materiales de construcción que se acumulan en los últimos años parece claro que las nuevas mezclas de cemento y hormigón van a tener un papel protagonista. Se busca mejorar sus propiedades y hacerlos más baratos utilizando populares ingredientes pero también que sean capaces de generar electricidad y analizar los edificios.
La última novedad en ese sentido proviene de la Universidad de Princeton. Allí, el equipo de investigación dirigido por Reza Moini, uno de los más prolíficos del panorama internacional, ha presentado un nuevo material a base de cemento que es 5,6 veces más resistente a las grietas inspirándose en la arquitectura de la capa externa de los huesos humanos.
Los ingenieros se fijaron en la densa capa exterior del fémur humano, especialmente fuerte y resistente a las fracturas, para manipular la estructura del material y conseguir mejoras significativas sin añadir ningún material adicional como fibras o plásticos. En un artículo publicado en Advanced Materials, el equipo detalla cómo han conseguido una arquitectura tubular para aumentar la resistencia ante la propagación de grietas y mejorar la capacidad de este nuevo cemento a la hora de deformarse sin fallos repentinos.
Resistencia y tenacidad
En el campo de la ciencia de materiales, donde se están haciendo avances fundamentales para el futuro de la construcción, resulta clave comprender propiedades como la resistencia o la tenacidad. La resistencia mide el estrés que un material puede soportar antes de que ocurra una deformación, mientras que la tenacidad determina la capacidad de un material de absorber energía antes de fracturarse, tras ser sometido a fuerzas externas.
Ambas propiedades mecánicas compiten entre sí en materiales como el cemento, que presenta una gran resistencia pero está limitado por su baja tenacidad a la fractura, sobre todo en comparación con otro tipo de materiales como el acero. En concreto, materiales como el hormigón, el mortero o la pasta de cemento son frágiles frente a las fracturas, ya que tienen una capacidad limitada de disipar la energía durante el inicio y la propagación de una grieta.
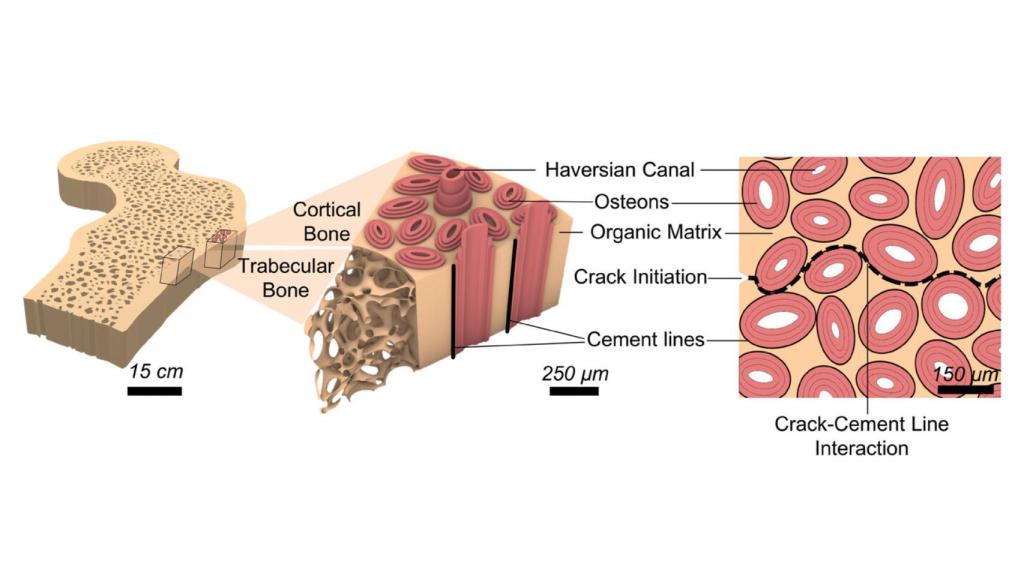
Esquema de los huesos corticales Omicrono
Por eso, Reza Moini y Shashank Gupta, estudiante de doctorado en Princeton y coautor del artículo, se han fijado en las posibilidades que ofrecen los materiales naturales. Muchos de ellos logran una gran resistencia y tenacidad "ensamblando componentes modestos en disposiciones complejas y arquitecturas jerárquicas".
"Uno de los problemas de la ingeniería de materiales de construcción frágiles es que fallan de forma abrupta y catastrófica", explica Gupta en un comunicado de prensa. Para solventarlo, los investigadores se han inspirado en el hueso cortical, en el exterior del fémur. Éste está formado por osteones, componentes tubulares elípticos incrustados débilmente en una matriz orgánica. Eso permite desviar las grietas alrededor de los osteones, evitando un fallo abrupto y aumentando la resistencia al agrietamiento.
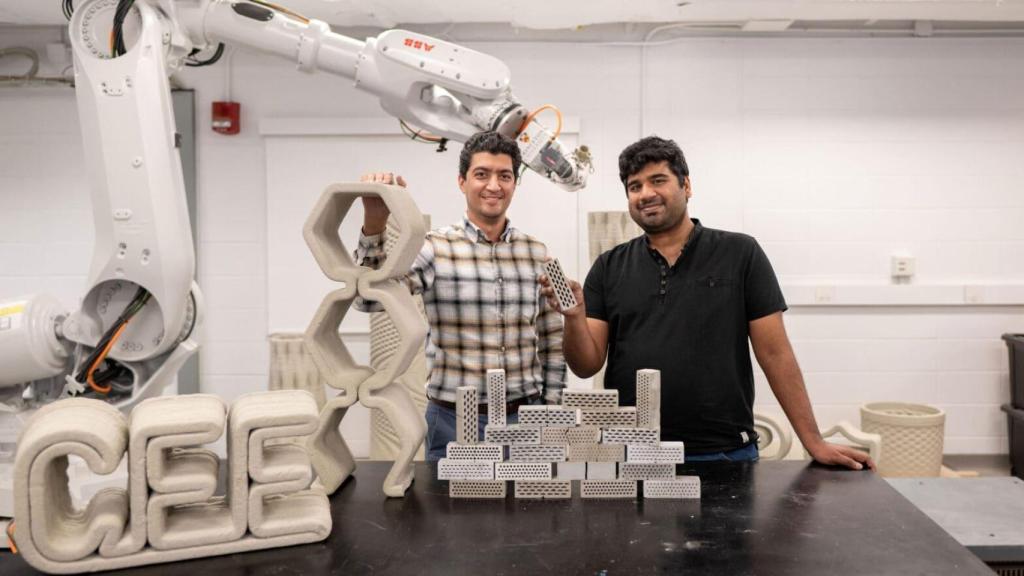
Reza Moini y Shashank Gupta junto al brazo robótico de impresión 3D y sus materiales de cemento Omicrono
"Utilizamos principios teóricos de la mecánica de la fractura y la mecánica estadística para mejorar las propiedades fundamentales de los materiales 'por diseño'", explica Moini. El método pasa por incorporar tubos cilíndricos y elípticos dentro de la pasta de cemento, capaces de interactuar con las grietas. En caso de aparecer una fisura, la estructura reacciona creando un mecanismo de endurecimiento escalonado: la grieta queda atrapada por el tubo y luego se retrasa su propagación.
El equipo descubrió que esta interacción reforzada entre la grieta y el tubo inicia un mecanismo de endurecimiento escalonado, en el que la grieta queda primero atrapada por el tubo y luego se retrasa su propagación, lo que provoca una disipación de energía adicional en cada interacción y paso. "Lo que hace único a este mecanismo escalonado es que cada extensión de la grieta está controlada, lo que evita un fallo repentino y catastrófico", sostiene Gupta. "En lugar de romperse de golpe, el material soporta daños progresivos, lo que lo hace mucho más resistente".
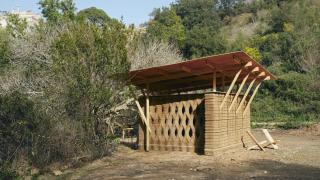
Omicrono
Utilizando enfoques experimentales y teóricos y tras desarrollar una técnica de fabricación híbrida (impresión 3D y moldes de uretano), los ingenieros diseñaron materiales tubulares a base de cemento con el mecanismo de endurecimiento por agrietamiento escalonado. Dependiendo del tamaño, la orientación y la forma de los tubos de la estructura se modificaban las propiedades. Tras varias pruebas, Moini y Gupta consiguieron un diseño que mejoraba la tenacidad global a la fractura del material hasta 5,6 veces en comparación con la pasta de cemento convencional.
"Este enfoque nos proporciona una poderosa herramienta para describir y diseñar materiales con un grado de desorden a medida", afirma Moini. "El uso de métodos de fabricación avanzados, como la fabricación aditiva, puede favorecer aún más el diseño de estructuras más desordenadas y mecánicamente favorables y permitir la ampliación de estos diseños tubulares para componentes de infraestructuras civiles con hormigón".
Escamas de pez
El avance se produce apenas unos días después del anterior del mismo laboratorio, también inspirado en la naturaleza. En este caso es el pez celacanto el que está detrás del hallazgo, ya que sus escamas forman una estructura de doble hélice que aporta mayor resistencia ante fracturas. Moini y su equipo aplicaron este inteligente diseño natural en una nueva técnica de construcción con hormigón impreso en 3D.
Para empezar, el esquema de diseño se basa en cambiar ligeramente la orientación de cada pila para crear una disposición de doble hélice o, dicho de otra forma, dos capas ortogonales retorcidas a lo largo de la altura. Esta idea se puede apreciar mejor en las imágenes compartidas por la universidad, donde se puede ver al robot imprimir con formas zigzagueantes que terminan formando patrones de onda en la columna según se va elevando.
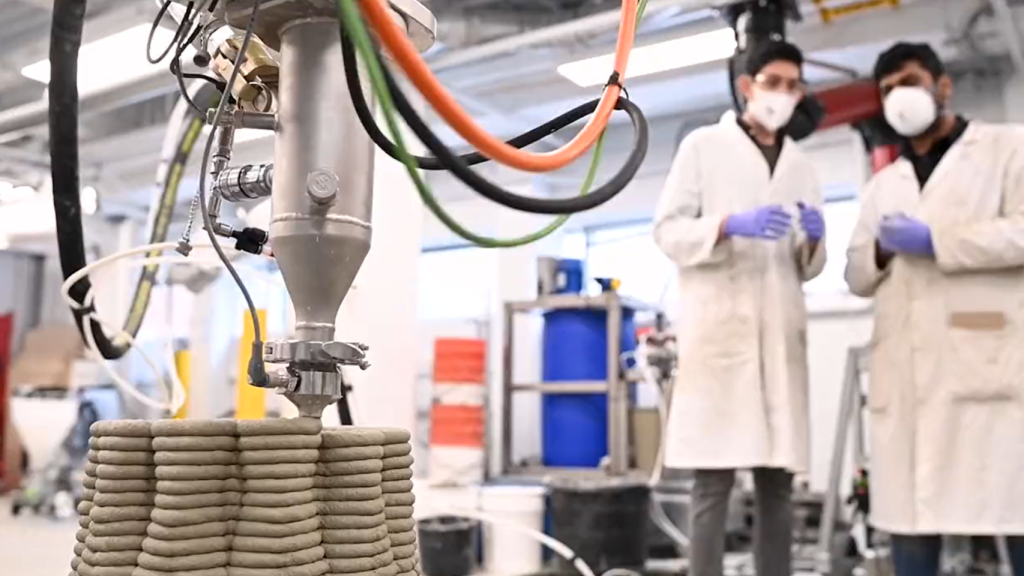
Brazo robótico con doble sistema de extrusión Omicrono
Así se crean vigas con mayor resistencia a las grietas. Si se aprecia en proyectos de impresión 3D de hormigón, la boquilla del robot va depositando el material en línea recta, una encima de otra, a diferencia de los relieves geométricos que proponen en Princeton.
En este caso, en la boquilla se ha instala un sistema doble de extrusión para fusionar dos componentes segundos antes de depositar la mezcla en la estructura. El primer elemento es el hormigón y, el segundo, un acelerador químico. Estos materiales se mezclan para acelerar el proceso de curado del hormigón, al tiempo que garantizan un control preciso sobre la estructura, minimizando la deformación. El resultado son paredes de hormigón impresas en 3D con una resistencia a las grietas hasta un 63% superior que si estuvieran construidas con hormigón convencional.