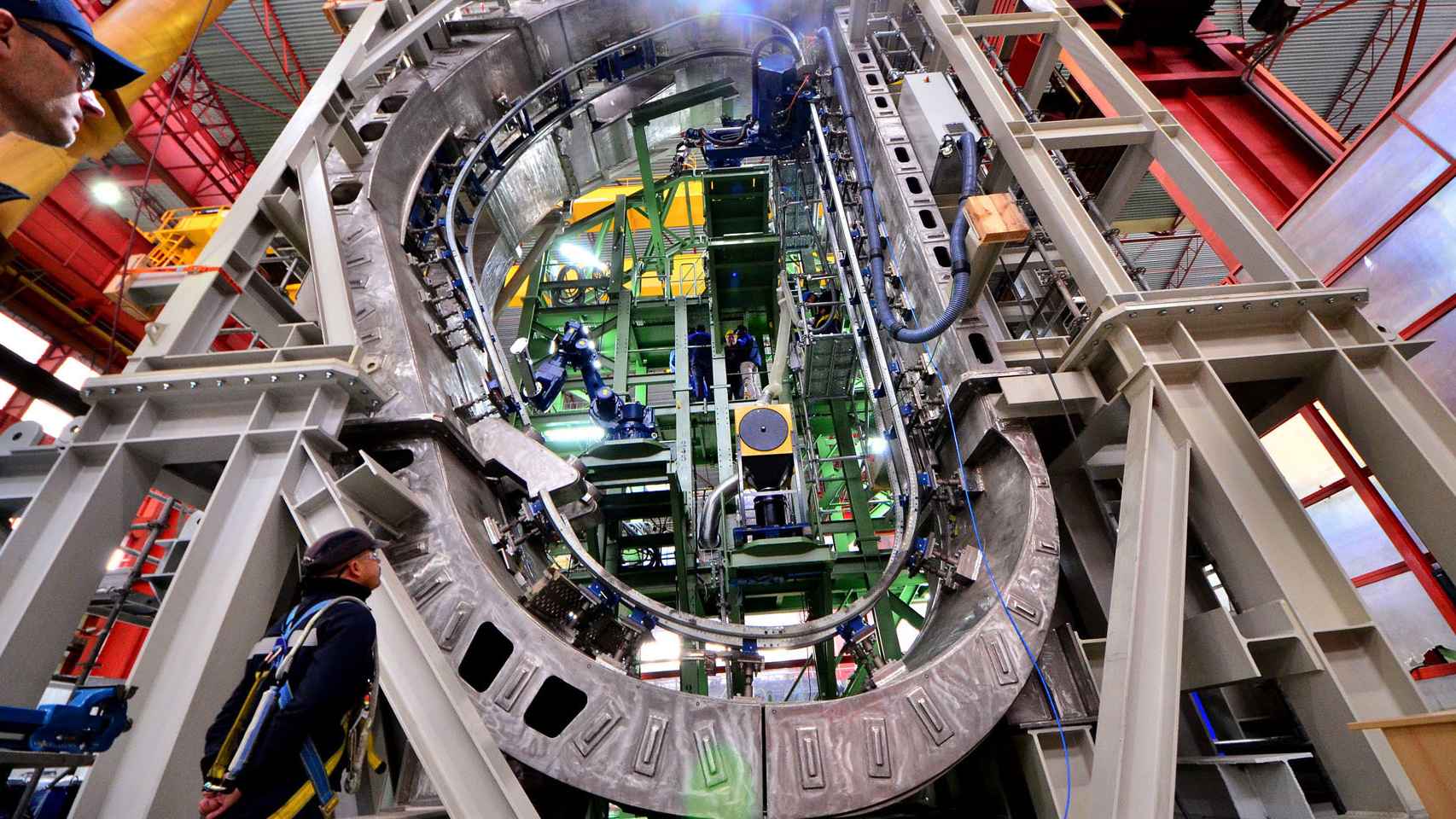
Maqueta a tamaño natural que ENSA montó en su sede para los ensayos.
El mayor experimento de fusión nuclear del mundo estará 'sellado' por una empresa cántabra
ENSA desarrolló las herramientas y procedimientos en un primer contrato y empezará a unir las partes de la vasija en marzo.
8 septiembre, 2021 03:11Noticias relacionadas
La más faraónica obra de la humanidad se está construyendo piedra a piedra (metal a metal) en Cadarache (Francia), para traer el mismísimo Sol a la Tierra a mediados de esta década.
El International Thermonuclear Experimental Reactor (ITER) es un enorme proyecto de tecnología avanzada, para construir un reactor de fusión nuclear, en el que participan Estados Unidos, la Unión Europea (es decir, todos sus países), China, Rusia, Japón, la India y Corea del Sur.
El propósito del reactor no es propiamente producir energía para consumo. Su objetivo es demostrar que es posible generar más energía de la que consume la operación. Después llegarán los reactores operativos, capaces de suministrar grandes cantidades de electricidad y el del ITER será desmantelado.
Los siete grandes socios aportan financiación y, lo que es más importante, la fabricación de la mayoría de las piezas y elementos para la construcción, elevando así el nivel científico-tecnológico de sus empresas participantes y revirtiendo la inversión en sus propias economías.
El pasado mes de mayo, ITER anunció la asignación de un contrato para soldaduras de alta precisión a la española Equipos Nucleares (ENSA), compañía pública perteneciente a la SEPI y especializada en trabajos relacionados con instalaciones nucleares. ENSA tiene su sede en Maliaño, Cantabria.
"Bueno, no dejamos de ser una calderería…", aclara con un toque de humor su directora de desarrollo de negocios, María Eugenia Vega Antolín, en conversación con D+I.
Una peculiar calderería en la que se dedican a "fabricar componentes de gran tonelaje, con una normativa muy exquisita para poder montarlos en una central nuclear".
"La verdad es que cuando dices dónde trabajas, equipos nucleares, la gente dice ¡uf!, eso debe de ser malísimo…", añade Vega, lamentando "la falta de información" que fomenta el miedo a lo desconocido.
En el caso del futuro reactor del ITER se trata de generar una reacción opuesta a la de las centrales nucleares de fisión: en vez de 'romper' átomos de pesados metales radiactivos, liberando radiación, se fusionarán dos isótopos de hidrógeno para generar átomos de helio.
Soldaduras de alta precisión
En el proceso se unirán un átomo del isótopo deuterio, que tiene un protón y un neutrón, con uno de tritio, que tiene un protón y dos neutrones. Al fusionarse forman un átomo de helio (gas inerte), con dos protones y dos electrones, y liberan energía y un neutrón.
Es el mismo proceso que genera la energía en el interior del Sol. Sólo que en el núcleo del astro rey las temperaturas máximas alcanzan unos 15 millones de grados (6.000 grados en la superficie solar), mientras que en la vasija del ITER se generará un plasma que alcanzará hasta los 150 millones de grados.
El plasma se moverá a altísima velocidad dentro de la vasija por la acción de tres potentes campos magnéticos, generados por bobinas poloidales, electroimanes toroidales y un solenoide.
Y en el interior de esa vasija, que cuando esté completada quedará sellada al vacío y no volverán a verlo ojos humanos hasta el día en que sea desmantelada, es donde ENSA tendrá que realizar sus soldaduras de alta precisión. Según especifica el ITER, se trata del "tercer contrato en importancia para las tareas de ensamblaje del tokamak".
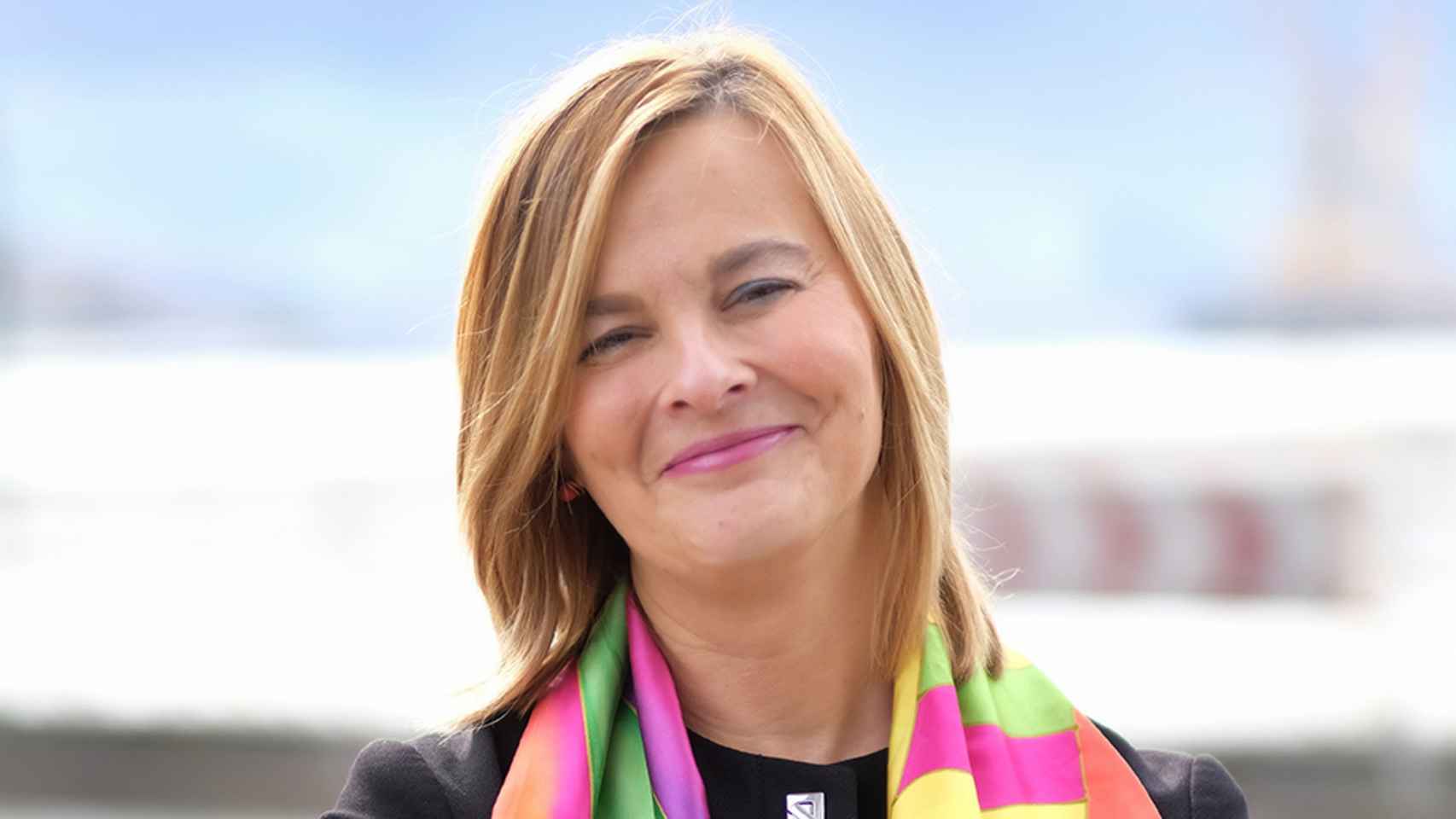
María Eugenia Vega Antolín, directora de desarrollo de negocios de ENSA.
"El contrato que hemos cerrado es para hacer el ensamblado de los nueve sectores y de los 54 puertos [de acceso] que lleva la vasija de vacío", explica Vega. "La vasija es como un neumático y de ahí salen todos los puertos", añade señalando en un gráfico los restringidos accesos al interior que estarán disponibles durante la operación del reactor de fusión.
El interior de la vasija estará recubierto de losetas protectoras, que 'absorberán' los neutrones liberados y sufrirán un desgaste. "Estos recubrimientos se irán cambiando durante la vida del reactor" y la operación se realizará mediante brazos robóticos "guiados por GPS", a través de los puertos.
Por cierto, parte de esos paneles recambiables están siendo "calificados aquí, en Cantabria también", en la empresa Leading Metal-Mechanic Solutions, informa Vega.
La vasija "tiene la configuración de un toro", contenida en "un tokamak, que es el sistema de contención". Está formada por "nueve sectores de 14 metros de alto", que irán llegando por separado y se ensamblarán en el ITER. "Hay que hacer todas las soldaduras de unión", entre los sectores, que son como gajos de la vasija. "Y las de todos esos puertos", precisa Vega.
Tecnología propia
Los especialistas de ENSA irán trabajando desde el interior de los sectores, a medida que lleguen. "Para poder hacer el trabajo hemos desarrollado sistemas remotos de soldadura y de inspección", indica. "Es una unión que sólo se puede trabajar desde dentro".
Los expertos soldadores "entrarían por los puertos y el reto es que tienes una vasija de doble pared y la mano del soldador prácticamente no tiene acceso [a ciertos puntos]. Utilizamos robots que son capaces de llegar y hacer la soldadura".
Tampoco hay acceso desde fuera "a la hora de hacer muchos de los controles, como por ejemplo una radiografía, para la que tienes que poner una película y algo que bombardea sobre ella", para comprobar la soldadura. Para eso ENSA utiliza sistemas "que despliegan la película por la parte de atrás".
Pero estas son herramientas que la compañía cántabra ya había desarrollado con anterioridad, "no ligadas a la operación para el montaje de estos sectores en la planta", precisa Vega.
ENSA fue creada en 1973. "Nacimos al amparo del programa nuclear español, una apuesta del país, para construir nuevas centrales. Se apostó por que las ingenierías en España crecieran en conocimiento tecnológico nuclear y por tener un fabricante propio español, que pudiera suministrar equipos a las centrales españolas", explica.
Hoy su mercado "es el internacional. Y sí que competimos con otras empresas de nuestras dimensiones, con bastantes años detrás. Hay unas cuantas, no muchas, pero han ido surgiendo ahora bastantes competidores en Corea y en China".
Ese conocimiento acumulado ya le sirvió para conseguir un primer contrato con el ITER, en 2012, para desarrollar las herramientas, equipos y procedimientos que ahora se aplicarán para las soldaduras de alta precisión."La mayor carga de trabajo en todo este tiempo ha sido el desarrollo de los equipos. Poder asegurar que tenemos equipos fiables capaces de realizar esa soldadura", comenta Vega.
"Los hemos probado sobre maquetas. Tenemos una de 14 metros de alto [de tamaño natural], que simula dos partes de los sectores y sobre ella hemos probado todos los equipos y que somos capaces de soldar, de hacer los ensayos no destructivos, de mecanizar, donde corresponde, de situar bien las juntas de Unión… Está todo probado".
Una vez establecidos los procedimientos y desarrolladas las herramientas necesarias, el ITER sacó a concurso un nuevo contrato para realizar las soldaduras y "hubo varias empresas y consorcios en competición". ENSA volvió a ganarlo.
"Creo que el ITER finalmente valoró mucho el conocimiento que habíamos adquirido durante la fase de desarrollo", subraya la ejecutiva de ENSA, que volvió a ganar la licitación. El desarrollo anterior habría tenido que quedar a plena disposición de la compañía que lo consiguiera, fuera cual fuera.
Cuenta atrás
Regresando a las interioridades de la vasija, la previsión es empezar los trabajos de soldadura en marzo. "Lo que nos vamos a encontrar cuando lleguemos serán dos sectores. Empezaremos a hacer uniones y entonces llegará un tercer sector".
"Iremos completando la vasija. El trabajo en planta tiene prevista una duración de cinco años, en cuatro fases. Hasta dos años y medio después del inicio no se empezarán a ensamblar puertos", especifica.
ENSA, que cuenta con una plantilla de unas 500 personas (que se eleva a 650/700 sumando la compañía participada Enwesa, especializada en mantenimientos nucleares), estima que en los momentos de "pico de trabajo" dedicará a esta misión entre 120 y 130 personas.
"Parte de ese equipo son ingenieros, pero una parte muy importante, que es el grueso de la operación, van a ser montadores, soldadores y personal de ensayos no destructivos", precisa Vega. Todos altamente expertos. "A algunos los contrataremos localmente, pero siempre gente muy especializada y cualificada por nosotros", añade.
Las claves de la operación incluyen algunas destacables peculiaridades: "La primera es el material, un acero inoxidable 316, que así dicho parece de lo más común. Pero tiene una composición un poquito diferente. Se llama 'grado ITER'", dice.
El propio consorcio ITER controla y aprueba los materiales "para que funcionen de forma óptima con la fusión. Este es un material, en algunos casos, un poquito complicado".
"La segunda, es el acceso a la soldadura", continúa. "Hay muchos kilómetros de soldadura que hacer, con una apertura muy pequeñita, para que la aportación de material y, por lo tanto, de calor, sea mínima. Para evitar deformaciones".
"Además, lo tienes que hacer a distancia. Tienes que entrar por la abertura que te permite la pared interior, llegar hacia la exterior y ser capaz de soldar. Y hay parte de la soldadura que la tienes que hacer 'a techo', que tiende a descuelgues. La vasija no la puedes mover de la posición en la que está".
"Y la tercera dificultad, para mí, es la configuración", incide. "Tienes que tener un sistema de soldadura, que se vaya adaptando a todas las configuraciones que te encuentras. Hay [que unir] dos grandes piezas, de un tonelaje enorme, que es difícil casarlas".
"No es llegar con dos bordes de soldadura preparados, ponerlas una al lado de la otra y ya todo casa… Hay unas piezas de unión, unas juntas metálicas, del mismo material que las llaman space place. Se hace un control dimensional de cómo está esta parte y cómo está esta otra. Y entonces customizas la junta, o mecanizas los bordes, para adaptarte a lo que te encuentras", concluye.
La gran esperanza es que el reactor cumpla el propósito para el que ha sido diseñado y dé paso a una nueva forma de generar energía barata, aplicando una ingeniería para la que ENSA partirá con una buena base de conocimiento. María Eugenia Vega habla de futuros proyectos en España, Italia, Inglaterra, Estados Unidos… "Hay por ahí ya mucho movimiento de reactores de fusión".