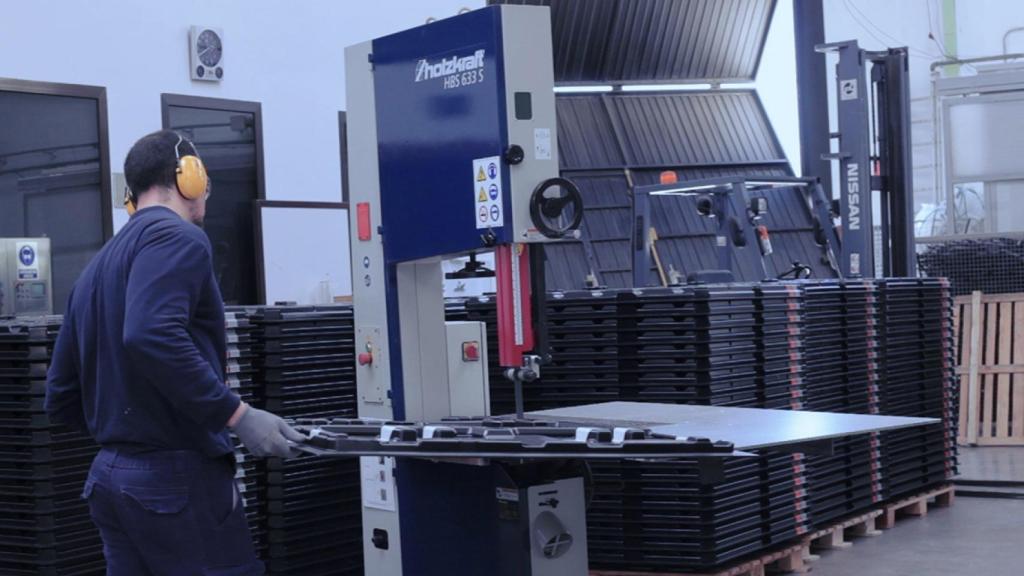
Sistema manual de medición del grosor de las placas de Flome.
La española que protege los motores de Ford y Jaguar con imagen en 3D
La firma de embalajes Flome utiliza la tecnología de calibre óptico de Nunsys para cuidar el traslado de piezas críticas en automociónrn
18 abril, 2019 07:00La fabricación de un coche es un rompecabezas complejo en el que intervienen múltiples fases y empresas. Los cobots, los sistemas de visión artificial y toda clase de elementos de internet de las cosas y sensorización son ya un componente habitual en los procesos de fabricación. Sin embargo, dentro de este amplio ecosistema, hay un elemento que a menudo pasa desapercibido pero es igual de crucial: el transporte de las piezas desde distintas procedencias y proveedores hasta las fábricas, donde definitivamente se ensamblan, y dentro de las mismas para terminar constituyendo el coche en cuestión. Si los requerimientos técnicos y tecnológicos de la fabricación son potentes, el transporte no se queda atrás.
Bien lo saben en la empresa valenciana Flome, donde llevan décadas especializados en el desarrollo y la fabricación de envases y embalajes a medida que garanticen la integridad de las complejas y delicadas piezas del sector de la automoción durante su transporte. Grandes marcas como Ford, Renault, Jaguar, Aston Martin, Volvo o Land Rover son algunos de sus clientes.
"El mundo del automóvil nos exige un alto grado de calidad en las piezas", explica Pedro Martín, responsable de proyectos de Flome, en todos los ámbitos. Incluso, en el grosor de los plásticos que protegen elementos tan críticos como los componentes de un motor. Para garantizar a sus clientes la calidad de sus plásticos, Flome tenía que sacar de la producción un número importante de las planchas termoconformadas que fabrican para trocearlas y controlar manualmente que el grosor exigido se mantenía en todas las partes de la pieza protectora.
Para mejorar este proceso -que hasta hace apenas un mes se hacía de forma manual- reducir el tiempo de tiempo de trabajo y maximizar la eficiencia se pusieron en contacto con la firma tecnológica Nunsys a través de una convocatoria que lanzó el Clúster del Envase y el Embalaje. La solución ha sido el desarrollo de un sistema de calibre óptico que parte de los principios de digitalización 3D mediante luz estructurada y que puede medir el grosor de cualquier parte de la pieza, y de cualquier pieza, sin necesidad de tener que romperlas.
Lo que han conseguido así es un "control más exhaustivo" que permite, en lugar de estudiar de 10 a 20 piezas de cada tirada, controlar el 100% de la producción gracias a una máquina y un software que se pueden situar en la misma línea de represetación y que, según explica Emilio Ribes, responsable del proyecto en Nunsys, permite digitalizar la pieza en cuestión por distintas capas.
El calibre se basa en el escaneo mediante luz estructurada, esto es, una técnica que ilumina los objetos sobre los que se proyectan patrones de blanco y negro. "El objeto deforma el patrón de luz y esa imagen es la que tratamos para convertirlo en un objeto 3D y calcular la distancia entre una cara y otra", señala Ribes. El sistema permite medir piezas muy grandes de más de metro, un punto muy importante en un sector en el que se trabaja con volúmenes tan grandes.
Así, Nunsys se ha encargado del procesado y la realización de la calibración a través del desarrollo de este softaware basado en la algoritmia de procesado de imágenes 3D de la compañía. El beneficio está claro: no solo se reducen los tiempos de análisis y se aumentan las garantías de calidad al poder comprobar las dimensiones de cada una de las piezas, sino que además se evitan pérdidas de productividad al no tener que trocear (y, por tanto, echar a perder) las piezas para medir su grosor como se hacía en el formato manual. «No nos consta que haya un sistema así aplicado a la logística del automóvil», asegura el responsable del proyecto en Nunsys, sobre esta incipiente herramienta.