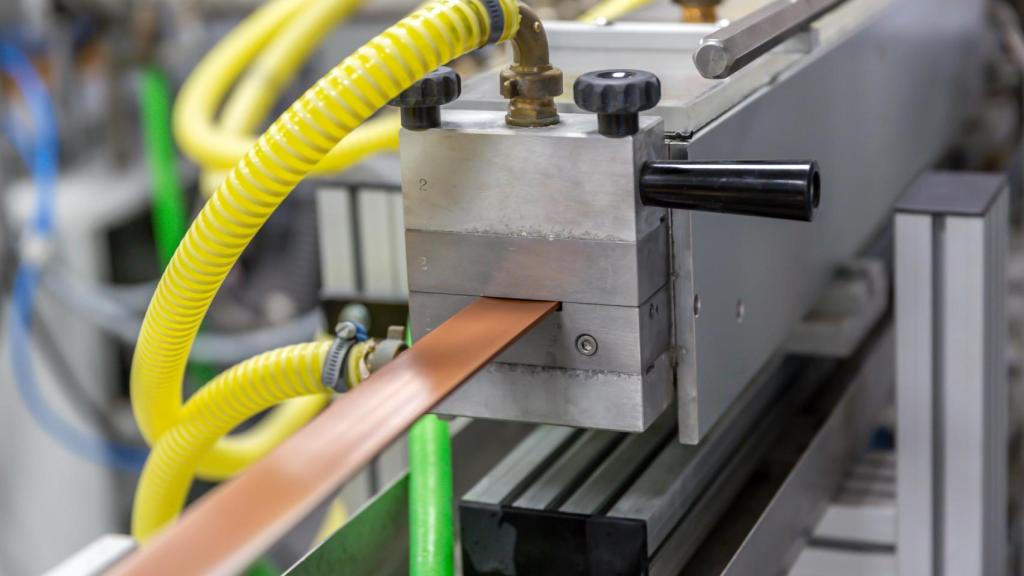
El proyecto 'Recerco' confirma que es posible valorizar los residuos cocidos de baldosas cerámicas y darles una segunda vida para una construcción más sostenible.
Cómo convertir residuos de baldosas cerámicas en nuevos materiales para una construcción más sostenible
Un proyecto de ITC y AIMPLAS, centrado en la economía circular, transforma estos residuos en nuevas baldosas y composites para perfilería de persianas o mobiliario urbano.
19 agosto, 2024 02:47La emergencia climática obliga a virar el modelo económico actual hacia una versión mucho más respetuosa con los recursos naturales. La economía circular se convierte, en esta tesitura, en un aliado de la sociedad para no comprometer la competitividad empresarial sin olvidar el compromiso con la sostenibilidad.
Los centros de investigación están desarrollando un papel crucial en este proceso donde la tecnología se convierte en el pilar transversal de nuevas soluciones encaminadas a generar valor de aquello que, a priori, ya no tiene una utilidad y está condenado a convertirse en un residuo.
El Instituto de Tecnología Cerámica (ITC) y el Instituto Tecnológico del Plástico (AIMPLAS) son el claro ejemplo de este valioso conocimiento. Ambas entidades están trabajando en el proyecto Recerco, que otorga una segunda vida a los residuos de baldosas cerámicas cocidas.
El proyecto avanza hacia el vertido cero en el sector cerámico, dado que un total de 15.000 toneladas de este residuo acaban cada año en el vertedero
En concreto, la propuesta está enfocada a valorizar los residuos generados en el proceso de fabricación de baldosas cerámicas, concretamente los denominados tiestos cocidos, es decir, baldosas de distintas tipologías, en su mayoría compuestas de arcilla roja.
Se persigue su incorporación, previo tratamiento, en la fabricación de nuevas baldosas cerámicas y, por otra parte, como agente de refuerzo de matrices poliméricas para obtener composites destinados a la construcción.
Reemplazar el contenido en arcilla
Los estudios realizados, en ambas aplicaciones, confirman que la introducción de este residuo como materia prima secundaria es viable técnicamente. Así, en el proceso de fabricación de baldosas cerámicas, es posible reemplazar buena parte del contenido en arcilla de la composición de las baldosas.
Por otro lado, en el caso de los composites, es posible sustituir completamente agentes de refuerzo tradicionalmente utilizados en la industria del plástico, como el carbonato de calcio o el óxido de titanio, por estos residuos, de forma que se pueden obtener composites termoplásticos y termoestables con propiedades idénticas o mejoradas.
En este sentido, en el marco del proyecto AIMPLAS ha aplicado los compuestos termoplásticos para fabricar perfilería de persianas en base PVC. Con los compuestos termoestables el centro tecnológico ha fabricado un macetero y un depósito, pero podrían utilizarse también en otras aplicaciones de exterior como mobiliario urbano.
El proyecto Recerco ha contado con el respaldo del Instituto Valenciano de Competitividad e Innovación (IVACE+i Innovación) a través del programa de Proyectos Estratégicos en Cooperación cofinanciado por la UE a través de los Fondos Europeos FEDER de Desarrollo Regional y la colaboración de las empresas Neos Additives, Miraplas, Giménez Ganga y Saxun, junto con los centros tecnológicos AIMPLAS e ITC.
Así, con esta iniciativa, la valorización de este tipo de residuo cerámico, que en la actualidad se destina a vertedero con un volumen anual de 15.000 toneladas, impacta positivamente en el sector de la construcción, dotándolo de productos más sostenibles y contribuyendo a lograr el vertido cero en el sector cerámico, otro de los grandes desafíos de esta potente industria española.