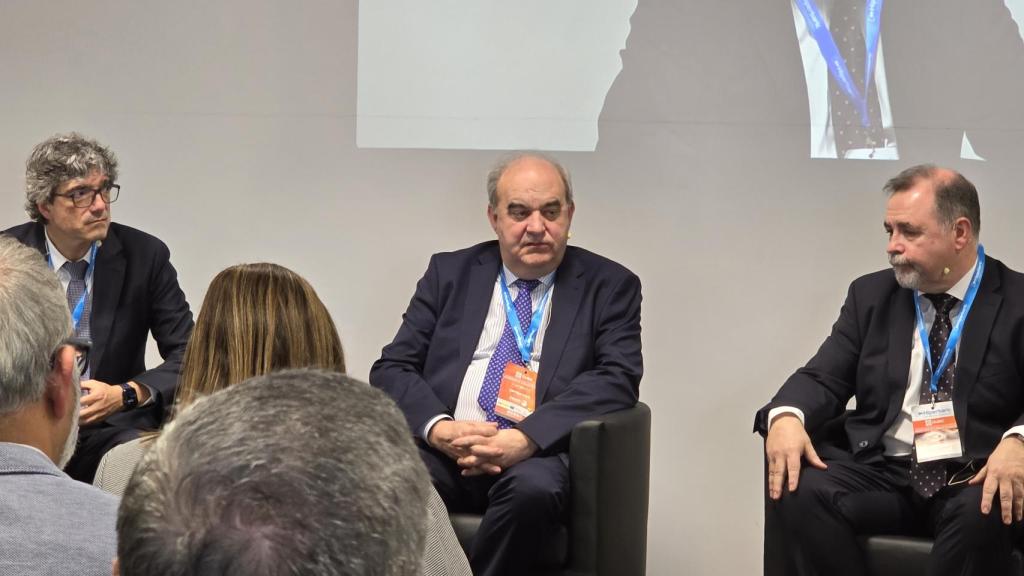
Los máximos dirigentes de Hiperbaric, Nanoker y Fagor Electrónica, en la presentación del proyecto DioSiC, en Burgos.
Chips con carburo de silicio policristalino: el proyecto DioSiC planea fabricarlos por primera vez en España
Tres empresas, Hiperbaric, Nanoker y Fagor Electrónica, anuncian en Burgos las tecnologías que abaratarán sus semiconductores más eficientes.
3 marzo, 2024 02:00Europa se ha despertado bruscamente de los sueños globalistas y ha comprendido que necesita ser capaz de producir sus propios chips. Admite la secretaria general de Innovación, Teresa Riesgo, que “España y Europa están bien en ciencia, pero mal en innovación”. Y por supuesto, fatal en convertir ideas en producción destinada al mercado real.
“Bosch va a poner una planta para la fabricación de carburo de silicio, con tecnología patentada en Francia. Pero van a desarrollar un producto [para semiconductores] muy caro. Nosotros estamos yendo un paso más allá. Queremos ser mucho más disruptivos”, aclara Ramón Torrecillas, consejero delegado de Nanoker.
Las palabras clave son “nosotros” y “carburo de silicio”.
Ese “nosotros” se refiere a tres empresas españolas embarcadas conjuntamente en el proyecto DioSIC, acogido al PERTE chip, con el objetivo de fabricar semiconductores de alta potencia. Son la citada Nanoker, con sede en Oviedo; Fagor Electrónica, con sede en Mondragón; e Hiperbaric, con sede en Burgos y anfitriona de la puesta de largo del proyecto, a la que asistió D+I - EL ESPAÑOL.
Y la clave tecnológica es ese “carburo de silicio”, también denominado SiC, con el que el proyecto confía en generar un avance muy significativo en la tecnología de fabricación de semiconductores, que pondrá a España en un mapa en el que, ahora, “no estamos”, dice Torrecillas.
El proyecto DioSIC (acrónimo de Diodo y SiC) persigue la ambiciosa idea de generar un nuevo material, carburo de silicio policristalino, para utilizarlo como sustrato sobre el que montar semiconductores en una fábrica española. Serán dispositivos más eficientes en el uso de energía y en gestionar el calor. Producto real para el mercado.
El proyecto cuenta con la colaboración científica de una selecta media docena de centros de investigación. Tres de ellos del CSIC (Centro Nacional de Microelectrónica, Centro de Física de Materiales y Centro de Nanomateriales y Nanotecnología), el CEIT vasco y otros dos pertenecientes al instituto alemán Fraunhoffer (Institute for Integrated Systems and Device Technology -IISB; y Center for Silicon Photovoltaics-CSP).
PERTE chip
DioSiC se acoge a la convocatoria Misiones del CDTI para el PERTE Chip, que aporta el 66% de un presupuesto de 3,5 millones. Jaime Martorell, comisionado del PERTE, confía en que esta iniciativa ayude a “recuperar la capacidad de fabricación en Europa que hemos ido perdiendo con los años”. La producción europea actual de chips es sólo el 8% del total mundial y aspira a llegar al 20%. También Estados Unidos flojea, con el 12% anual ahora y el propósito de llegar al 25%.
El mérito del carburo de silicio, que las tres compañías confluyentes esperan explotar como ventaja competitiva, es que se trata de una base para insertar los transistores, con “grandes características eléctricas y térmicas muy superiores a los dispositivos de silicio”, expone Mikel Pérez, director de I+D de Fagor Electrónica.
Pero, “el problema es que cuesta más de 10 veces más” que el silicio, contrapone el propio Pérez. “Desarrollar una tecnología que permita reducir el coste del sustrato casi a la mitad, va a hacer que los productos sean muy, muy competitivos. Es la ventaja de este proyecto”.
El reparto de tareas entre los tres socios es fundamental. Les quedan por delante “26 meses”, dice Hernando, para completar el proyecto definido a tres años, cuya cuenta atrás empezó a correr en 2023.
Nanoker, especializada en trabajar con nanomateriales cerámicos avanzados, es dueña de 17 patentes y “tecnologías propias para densificar material nanoestructurado”, subraya Torrecillas. Se encargará de producir el carburo de silicio policristalino, utilizando un proceso de densificación SPS (Spark Plasma Sintering).
Alta presión y temperatura
En paralelo, Hiperbaric desarrollará una máquina específica, capaz de someter a esa sustancia a una presión de 2.000 bares, dentro de un horno que puede alcanzar los 2.000 grados. “Es un postprocesado para conseguir un sustrato mucho mejor mediante la tecnología de alta presión y alta temperatura”, detalla Andrés Hernando, CEO de Hiperbaric.
La tecnología denominada HIP (Hot Isostatic Pressing, o prensado isostático en caliente) mejora las características del material: hace más homogénea la microestructura, consiguiendo una densidad cercana al 100%. Hiperbaric aplica también HIP para optimizar la estructura de piezas fabricadas con impresoras 3D, eliminando microporos, y para el tratamiento de alimentos, matando las bacterias. En este caso el elemento que utiliza para ejercer la presión es agua. Para el carburo de silicio policristalino usará gas argón.
En cuanto a Fagor, su papel en DioSiC será fabricar los chips. Pero hasta llegar ese momento tiene unas cuantas cosas que hacer por el camino. “Nosotros tenemos que definir cuáles son las condiciones que debe cumplir el sustrato para ser válido”, declara Pérez.
“Ahora estamos trabajando con dispositivos [semiconductores basados en carburo de silicio] que no son policristalinos, sino monocristalinos, para entender qué problemas nos vamos a encontrar cuando utilicemos el sustrato policristalino y definir las bases del desarrollo”, añade.
Torrecillas lo resume de la siguiente manera: “Hay claramente dos líneas que confluyen. Por un lado, Fagor, que utiliza producto de nuestra competencia en el mercado para validar su propio diseño [chips con carburo de silicio]. Mientras, Hiperbaric y Nanoker estamos desarrollando en paralelo, una tecnología distinta y dentro de un año, más o menos, tendremos que suministrarles lo mismo que están adquiriendo ahora en el mercado, pero mejorado. Y ellos, Fagor, evaluarán si lo hemos hecho bien o mal”.
Fagor ya fabrica para la automoción
Fagor Electrónica ya fabrica en la actualidad chips, diodos y tristores, para la industria de automoción. Ahora “tiene que hacer algo difícil, trabajar como si ya tuviera los sustratos definitivos y luego cambiar lo que hace en [carburo de silicio] monocristalino por el policristalino”, resume Torrecillas.
“Nos va a decir qué va bien y qué va mal. Tendrá que haber una retroalimentación, para saber qué tenemos que mejorar y qué va mejor en lo nuestro, en comparación con lo que ha estado utilizando”, concluye.
Los plazos suponen un primer año de puro desarrollo de las tecnologías implicadas en el proyecto. Después será el momento de combinarlas y depurar resultados, con el objetivo de lograr, de entrada, una reducción del 30% en el coste de producción de semiconductores de alta potencia, que además sean capaces de mejorar un 35% la eficiencia, en comparación con lo existente.
“En España no existe una cadena de valor completa para la fabricación de chips, ni siquiera en silicio. Mucho menos en carburo de silicio. Pero España no pretende hacer lo mismo que están haciendo ya otros países porque sería ridículo. Nosotros pretendemos salir al mercado un paso más allá, con carburo de silicio, que es donde está el valor real”, asevera Torrecillas.
“Esto supone ponerse en el mapa tecnológico como un país con capacidad no sólo para generar chips propios, sino controlando muchos más eslabones en la cadena de valor. No hay nadie que esté utilizando una tecnología disruptiva que salga más barata. Nosotros estamos intentando eso, con una tecnología de sustrato que no tiene nadie en el mundo, para que Fagor pueda seguir haciendo lo que está haciendo, de manera mucho más competitiva en el mercado”, afirma con rotundidad.
“Lo bueno es que Fagor ya está en el mercado europeo de automoción” señala Pérez. “Este proyecto se vende solo, porque después de terminarlo el siguiente paso, que es el importante, es vender producto”.
No obstante, evitemos equívocos, se trata de fabricar cierto tipo de semiconductores, no procesadores para CPUs de ordenadores, o GPUs, procesadores gráficos, ahora muy codiciados para el entrenamiento de inteligencia artificial, lo que ha disparado la valoración del principal fabricante, Nvidia, multiplicándola por 20 en cinco años.
“Fagor es reconocido en el mercado como fabricante de dispositivos de potencia. Fabricar dispositivos de microelectrónica es otra cosa completamente diferente. A Fagor le sería imposible, a corto o medio plazo meternos ahí”, confiesa Pérez.
Una planta para fabricar microelectrónica tiene “un coste inasumible para una empresa como nosotros”, afirma el director de I+D, de Fagor, aludiendo a las cifras que menciona Martorell, comisario del PERTE: hacen falta entre 20.000 y 30.000 millones, “y cinco años”, para construir una fábrica de procesadores.
El plan recién anunciado por el ministro Escrivá de crear una Sociedad Española para la Transformación Tecnológica (SETT), sólo suma unos 20.000 millones de euros y eso incluye absorber los 12.250 asignados al PERTE chip. Si el proyecto DioSiC ya supone asumir un cierto riesgo, la posibilidad de pensar en una fábrica de procesadores al estilo de las de Intel es hoy, sencillamente, inimaginable hasta para el propio Estado español.