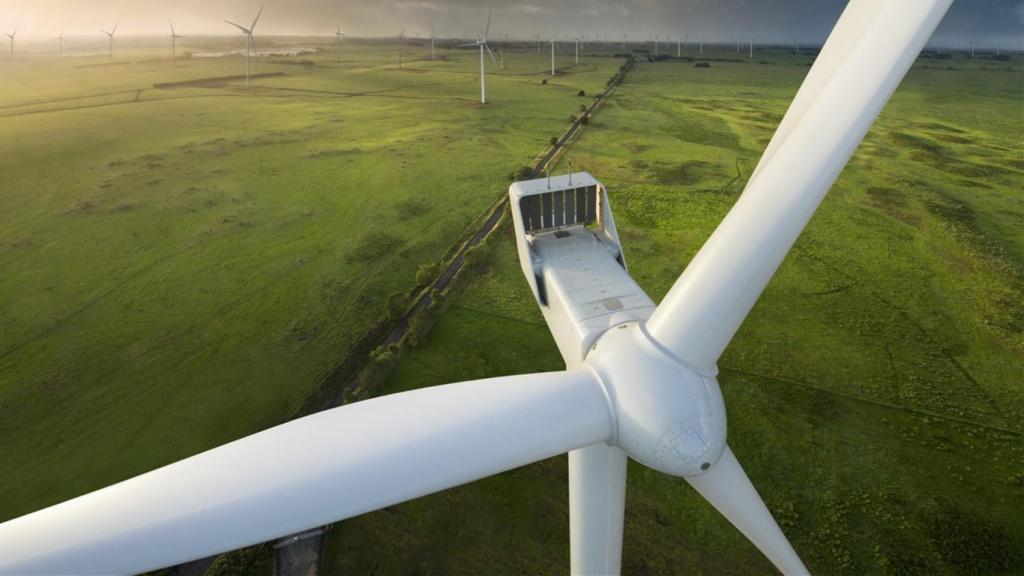
Un parque eólico Omicrono
Aerogeneradores de 100 metros impresos en 3D: la innovadora técnica para tener energía más barata
En vez de trasladar la turbina fabricada, la start-up Orbital Composites propone desplazar una fábrica de impresión 3D hasta el lugar de instalación.
22 agosto, 2023 01:59La impresión 3D se postula como la solución para fabricar más rápido y con menos costes toda clase de productos, desde pequeñas herramientas necesarias en hospitales de España, pasando por grandes construcciones como puentes en los canales de Ámnsterdan, hasta los futuros hábitats de Marte. Sus ventajas pueden también rebajar el precio de la luz generada por los aerogeneradores más grandes del mundo, al abaratar su proceso de fabricación y materiales.
Transportar un aerogenerador de más de 200 metros de altura desde la fábrica hasta el punto elegido para su instalación no es sencillo. Las carreteras hacia zonas montañosas o su transporte por mar pueden complicar la puesta en marcha de estos gigantescos molinos, una dificultad que encarece el coste final de esta energía renovable.
Como solución a este sobrecoste, algunos proyectos apuestan por diseños modulares en los que la estructura se compone de múltiples piezas de menor tamaño y asegurando que la eficiencia no desmerece a las turbinas tradicionales más grandes. No obstante, la impresión 3D in situ podría ser otra alternativa con la que abaratar costes sin renunciar a las megaconstrucciones eólicas.
Imprimir in situ
En vez de transportar con lentitud y dificultad el producto ya fabricado, sería la fábrica la que se desplazara hasta el lugar elegido, según lo que propone la start-up Orbital Composites. "La mayoría de la gente no sabe esto, pero en realidad no quedan fábricas de palas eólicas en los EEUU", explica Amolak Badesha, director ejecutivo de la empresa a la revista FastCompany. Las piezas de gran tamaño se transportan desde otros países como China, aunque el proceso culmine en territorio estadounidense.
Orbital Composites ya utiliza su tecnología de impresión para crear piezas de drones y satélites. Sus ingenieros también están enfocados en múltiples objetivos espaciales, como la posibilidad de ensamblar y fabricar componentes en el espacio. La fabricación in situ facilita crear herramientas en estaciones espaciales, además de simplificar la construcción de las primeras colonias en la Luna o Marte.
Ver esta publicación en Instagram
Pero esta solución también puede facilitar la vida en la Tierra y abaratar la generación de energía renovable. Y es que uno de los alicientes que ofrece la exploración espacial es el uso en tierra firme de las tecnologías y avances que se desarrollan primero pensando en el espacio.
Las ventajas de este tipo de fabricación no se limitan al transporte, ya que la impresión 3D también es una manera de reducir los desperdicios en materiales. Este modo de fabricación aditiva solo aplica la cantidad exacta de material siguiendo la forma definida en los bocetos. Se calcula que con esta metodología es posible reducir el gasto de materiales en un 25%, al mismo tiempo que sería posible ahorrar entre un 10 y un 25% del coste de producción y transporte.
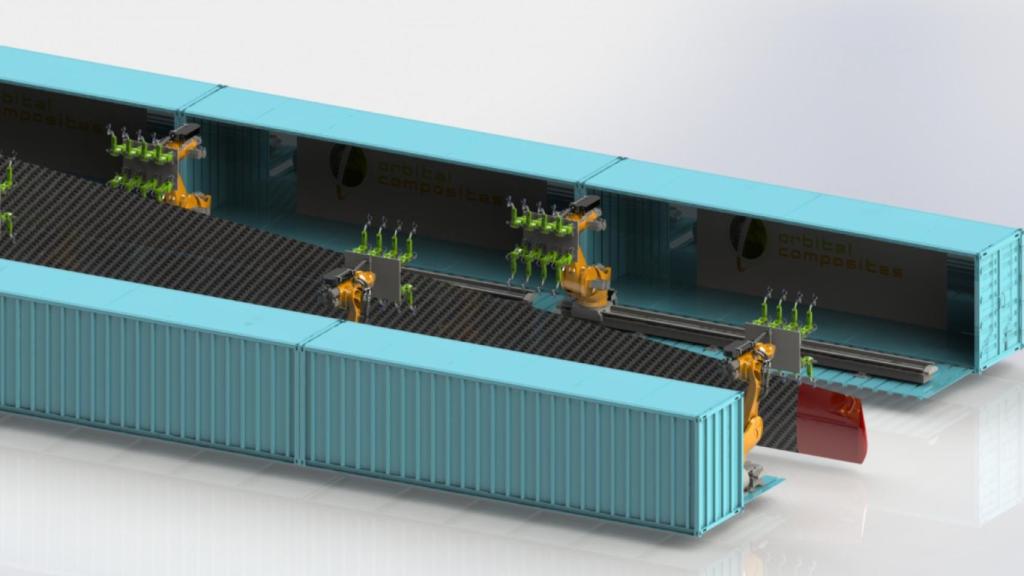
Robots impresores de 3D dentro de contenedor Omicrono
Dentro de grandes contenedores, las máquinas de impresión 3D se pueden transportar para, una vez en el destino, fabricar in situ las piezas necesarias, en concreto, las larguísimas palas. De esta forma, la compañía puede transportar por barco o carretera su sistema de impresión y crear uno o varios aerogeneradores cerca de dónde se van a instalar.
Primeras pruebas
En su primera demostración, a finales de este año, el equipo imprimirá una pala eólica de casi 9 metros de largo, una pieza que deberá demostrar su eficiencia y resistencia. Los ingenieros también están desarrollando nuevos procesos para imprimir en 3D la base y otras piezas de los aerogeneradores, aunque este objetivo se completará más adelante.
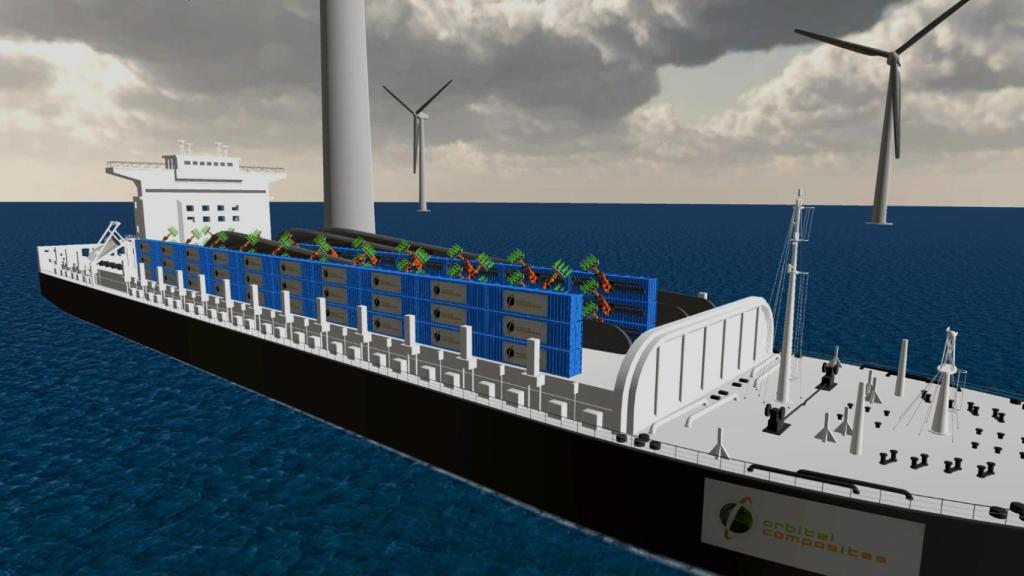
Fabricación en buques Omicrono
El siguiente paso a esa primera prueba se realizará a lo largo del próximo año y pretende probar un nuevo robot de impresión 3D capaz de viajar de un lado a otro en un sistema de cable mientras crea las palas, similar al sistema de cámaras móviles que hay en los estadios de fútbol. Esta solución aspira a alcanzar la escala de fabricación de palas de 100 metros sin necesidad de diseñar un sistema de impresión más extenso.
Con este nuevo robot, se han marcado un siguiente objetivo de 49 metros, al que seguirán palas de escala comercial casi tan largas como un campo de fútbol, lo que supone unos 90 metros de largo en la mayoría de los casos. En España, un aerogenerador de 100 metros de altura con aspas de hasta 70 metros de largo consigue generar 3,5 MW de potencia, alimentando las necesidades de aproximadamente 1.200 hogares en España según el gasto medio de la población.
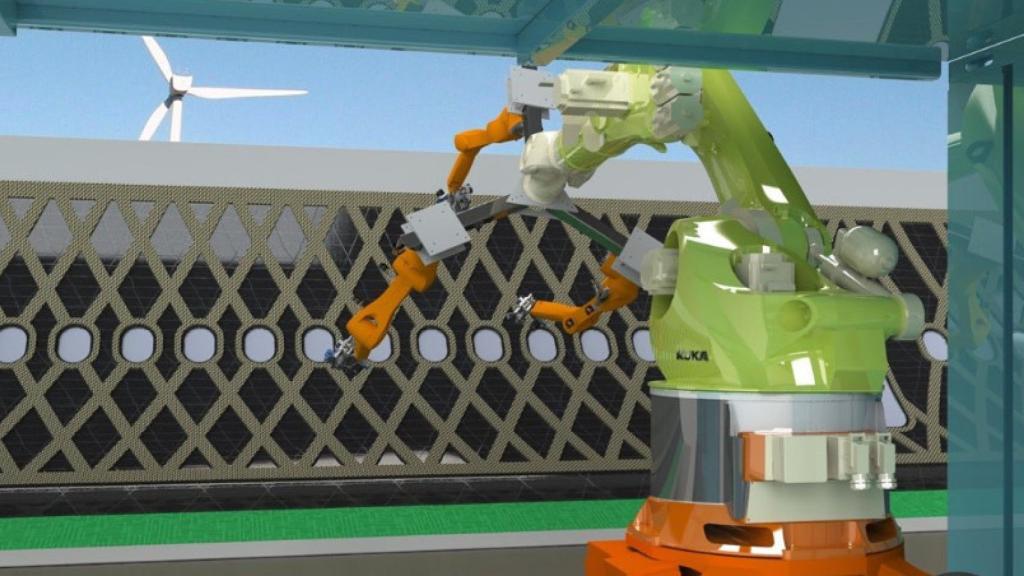
Impresión 3D in situ Omicrono
Otro de los avances que pretende alcanzar la compañía es la producción mediante materiales reciclables, algo que la mayoría de los fabricantes aún no utilizan. Para ello se han asociado con ORNL y la Universidad de Maine en un proyecto para desarrollar un método más ecológico de impresión 3D de moldes de palas de turbinas eólicas. Al introducir una materia prima de base biológica en su proceso de impresión de nanofibras de celulosa (CNF), el equipo cree que es posible reducir los costos de producción de piezas de gran formato en un 50%.