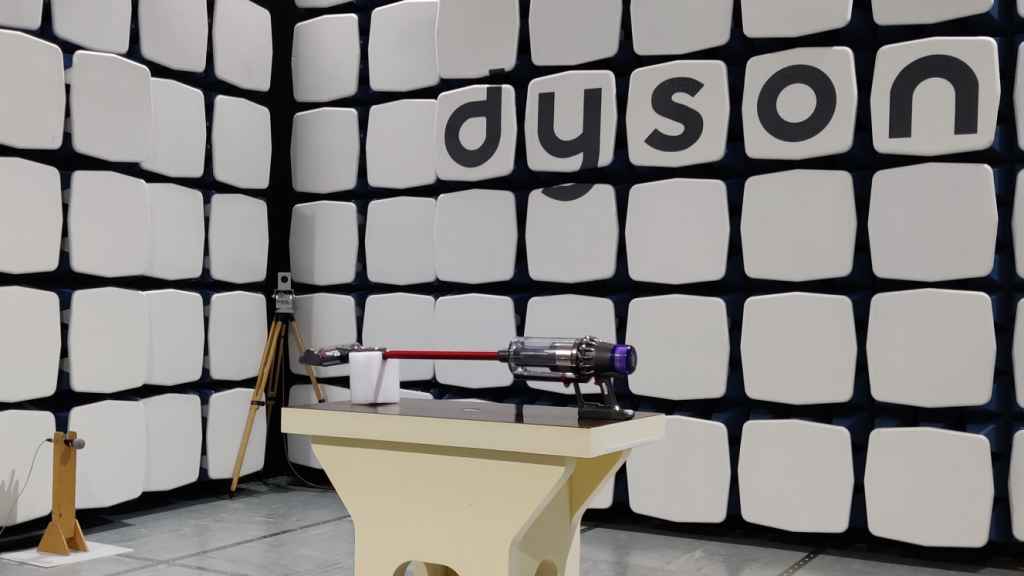
El laboratorio donde se miden las radiaciones electromagnéticas de los productos de Dyson Omicrono
En los laboratorios secretos de Dyson: así consiguen las aspiradoras más punteras del mundo
Visitamos la sede y el campus de I+D de Dyson en Reino Unido, donde miles de ingenieros diseñan y prueban los productos que marcan tendencia.
29 septiembre, 2023 01:51A día de hoy, Dyson es sinónimo de innovación en productos como aspiradoras, purificadores de aire, secadores de pelo, lámparas y hasta auriculares, el último producto que ha llegado a España. Pero todo empezó hace ahora tres décadas, cuando el ingeniero James Dyson asombró al mundo con el lanzamiento internacional de la DC01, la primera aspiradora sin bolsa. Lo hizo tras más de una década de investigación y después de fabricar a mano 5.127 prototipos, una hazaña que marcó a fuego la filosofía de una compañía que en la actualidad tiene más de 13.000 empleados repartidos por distintas instalaciones en lugares tan alejados como Inglaterra, México, Malasia o Filipinas.
En EL ESPAÑOL-Omicrono hemos viajado a Malmesbury, un discreto rincón de la campiña del suroeste de Inglaterra, en plena región de los Cotswolds, para conocer de primera mano la sede central y los laboratorios de I+D de Dyson, donde sus ingenieros desafían los límites de lo posible con nuevos desarrollos tecnológicos y mejoras en sus productos que hasta hace poco parecían ciencia-ficción. Mención especial merecen dos de sus últimos lanzamientos, el esperado Dyson 360 Vis Nav, "el robot aspirador más potente del mundo", según sus responsables, y el purificador para grandes espacios big+quiet, que proporciona aire limpio constante en habitaciones de hasta 100 metros cuadrados.
En un pequeño garaje de Malmesbury es donde empezó todo. Allí fue donde James Dyson, que ahora tiene 76 años pero sigue pendiente del día a día de la empresa, desarrolló su primer invento, el Ballbarrow, una versión modificada de una carretilla que usaba una esfera en lugar de una rueda, y el lugar que vio nacer el motor ciclónico de aspiradoras. Cerca de allí, entre verdes prados y edificios futuristas y bajo un secretismo digno de Misión imposible, tuvimos acceso a este monumento a la fusión definitiva entre el diseño y la ingeniería.
Nuevas soluciones
En las instalaciones del campus, donde también se encuentra el Instituto Dyson de Ingeniería y Tecnología (DIET, por sus siglas en inglés), el pasado y el futuro se dan la mano de una manera sorprendente. Entre prototipos de última generación, laboratorios de robótica avanzada y gigantescas máquinas de impresión 3D, también tienen su hueco varios iconos de la ingeniería, instalados en distintos emplazamientos para servir de inspiración a estudiantes y trabajadores.
En diversos puntos de este enorme complejo nos topamos con un motor Rolls-Royce para aviación diseñado en 1943, el primer asiento eyectable de un avión o el primer modelo de Mini partido por la mitad, que permite ver todos sus componentes internos. Pero lo más espectacular es el caza de combate supersónico English Electric Lighting colgado del techo de una de las cafeterías, como si fuera un elemento más de la decoración.
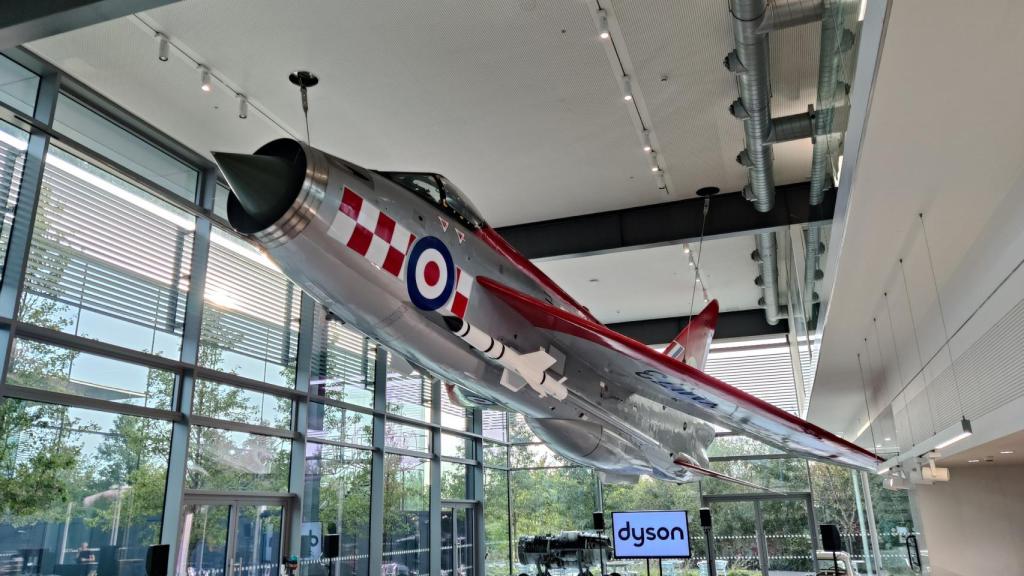
El caza English Electric Lightning en una de las cafeterías del campus de Dyson Omicrono
Y para saber cómo cala eso en el ambiente, marcado por la exigencia y el amor al detalle pero también por el permanente deseo de ir un paso más allá, lo mejor es hablar con uno de sus ingenieros. "Dyson empezó deshaciéndose de las bolsas de las aspiradoras. Pero no sólo queremos hacer máquinas con un alto rendimiento, sino que estén hechas para durar", explica Oliver Toogood, ingeniero sénior que lleva 5 años trabajando en la empresa británica.
Pese a su dilatada experiencia anterior con drones y coches eléctricos, este risueño ingeniero jamás se había topado con un entorno de trabajo como el de Dyson. "Normalmente, James tira las máquinas al suelo y las pisa o salta sobre ellas, para ver lo resistentes que pueden ser. Estos escenarios reales son los que nos obsesionan: ¿cómo podemos hacerla más ligera o más pequeña? ¿Cómo podemos usar menos plástico? ¿Cómo podemos hacer que cada milímetro de un producto trabaje para nosotros?".
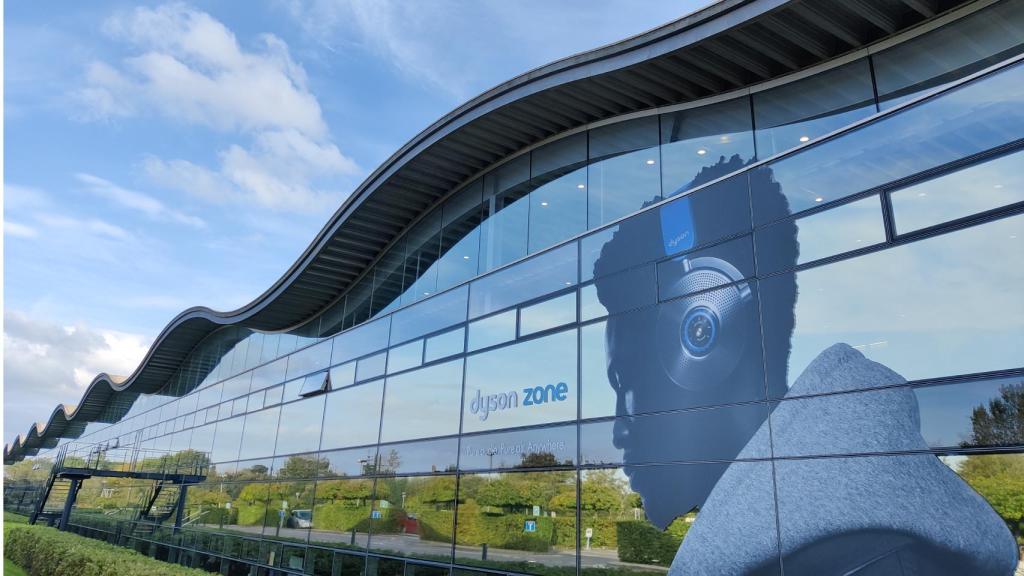
Uno de los edificios de Dyson en Malmesbury, Inglaterra. Omicrono
En palabras del propio James Dyson, "queremos solucionar los problemas que otros deciden pasar por alto", y eso está impregnado en todos los procesos de la empresa y en la mentalidad de sus trabajadores. Todo se rige por cuatro mandamientos, presentes en una gran lona en uno de los pasillos del campus: "nunca estés satisfecho, nunca te quedes quieto, nunca dejes de innovar, nunca te rindas". Para los ingenieros, esa manera de pensar, además de una obligación, es una motivación. "Disfruto de la libertad que me ha dado Dyson", dice Toogood. "Para mí venir aquí cada día es como estar en una enorme tienda de juguetes".
Laboratorios secretos
Para comprobar cómo trabajan para mejorar continuamente sus productos y dar con nuevas soluciones tecnológicas, nos adentramos en el intrincado laberinto de puertas, pasillos y zonas de alta seguridad de Dyson. Es el corazón de la investigación y el desarrollo de la compañía, que siempre ha buscado reducir al máximo la dependencia de terceros para poder acelerar los procesos y no comprometer la confidencialidad de sus productos.
Eso puede implicar una gran inversión inicial, pero a la larga es una manera de defenderse del siempre temido espionaje industrial y, lo que es más importante, les permite realizar pruebas con sus prototipos de inmediato, sin esperar a la disponibilidad de las instalaciones necesarias para obtener los certificados de seguridad y calidad.
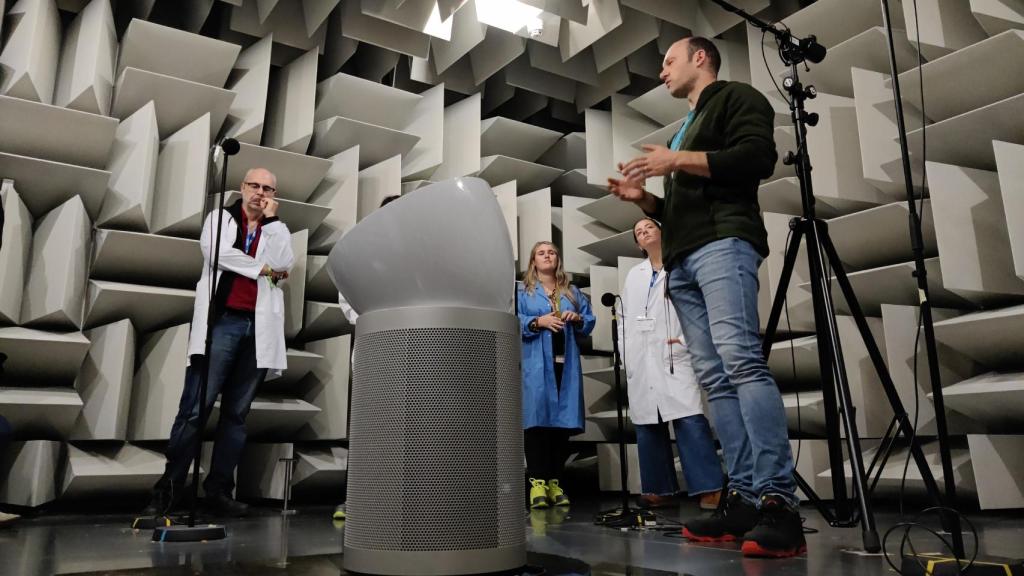
La cámara donde se analiza el ruido que producen los dispositivos de Dyson Omicrono
Con los responsables de cada área, visitamos la cámara semianecoica donde se mide el ruido que generan sus productos (y donde James Dyson grabó el audiolibro de su autobiografía, Invention: A Life), la sala en la que se mide la radiación electromagnética que emiten, las cámaras donde se testea la calidad del aire que ofrecen sus purificadores y donde se comprueba la eficiencia de las aspiradoras en distintas superficies y con distintos tipos de suciedad.
Entre todas las salas, dos llamaron poderosamente nuestra atención. Por un lado, el laboratorio de impresión 3D, donde las piezas y prototipos diseñados por ingenieros repartidos por todo el mundo cobran vida en gigantescas máquinas 24/7. Allí se prueban distintos materiales, como un plástico con partículas de alumino que lo hace más resistente, y salen a la luz los componentes de lo que acabará siendo una nueva iteración de alguno de los productos de Dyson.
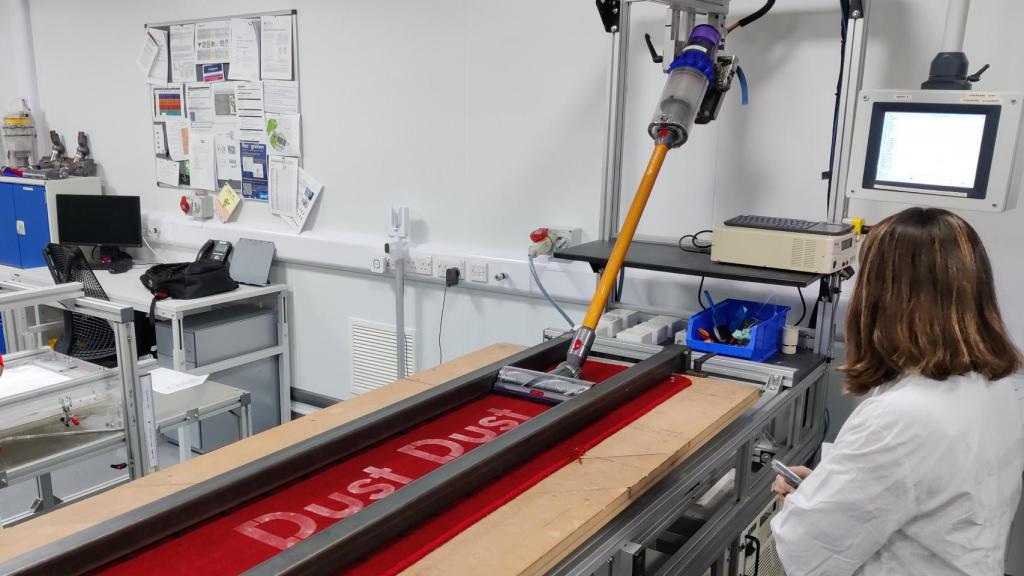
Sala de pruebas de las aspiradoras Dyson Omicrono
Por otro lado, está el laboratorio donde estudian el polvo y sus componentes, incluidos los ácaros del polvo, analizados a través de microscopios de barrido electrónico. Por las cápsulas con guantes incorporados puede parecer un lugar donde se estudian virus y bacterias mortales, pero aquí lo que se investiga son muestras de la suciedad doméstica de los propios trabajadores de Dyson, que permiten a sus científicos aportar información clave para que las aspiradoras y purificadores consigan mejores niveles de filtración y eliminación de residuos potencialmente dañinos para la salud.
Además de convertir el proceso de ensayo y error en un dogma infalible, quizá la clave del éxito de Dyson sea a lo estrechamente interconectados que están todos los procesos y divisiones de la compañía. Ingenieros, diseñadores y científicos colaboran mano a mano cada día, y eso les permite dar con soluciones que de otra manera no habrían encontrado.
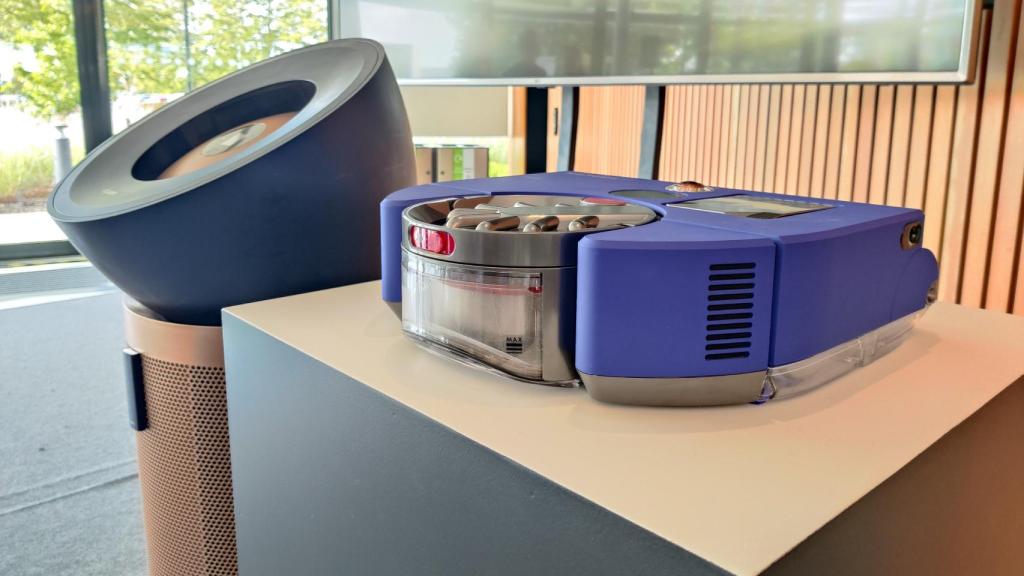
El robot aspirador Dyson 360 Vis Nav y el purificador big+quiet Omicrono
"Cada persona que trabaja en Dyson es un solucionador de problemas", resume Stuart Thompson, Design Manager de la compañía y nuestro guía a lo largo de buena parte de la visita. "Tanto si ese problema es de ingeniería, de suministros o de cómo comunicar los avances a la gente, el objetivo es el mismo: resolver el problema de la mejor manera posible. ¡Si no hubiera problemas por resolver sería bastante aburrido! Lo que yo hago es coger las cosas desde el primer borrador hasta la producción en masa, así que el tipo de problema va cambiando, pero lo fundamental es tener ese deseo de afrontar los desafíos y dar con la mejor solución".
El mayor desafío de los últimos años en Dyson tiene que ver con sus robots aspiradores, que todavía no han conseguido destacar tanto en el mercado como sus 'hermanos mayores' de mano. Para ello, la compañía ha ampliado sus instalaciones con la rehabilitación de dos enormes hangares de la RAF a pocos kilómetros de allí, en el aeródromo de Hullavington. Ese lugar es donde han diseñado y probado los últimos avances en software y sensores de mapeo y reconocimiento del polvo para dar vida al Dyson 360 Vis Nav, que hemos podido ver en acción y ya se ha lanzado en mercados como el australiano. Según nos cuentan, llegará a España en el primer trimestre de 2024.
Los ingenieros del futuro
El otro gran foco de Dyson ahora mismo tiene que ver con la educación. "Nuestro trabajo no es sólo diseñar nuevos productos, sino también inspirar a las nuevas generaciones de ingenieros. Con la James Dyson Foundation vamos a escuelas, explicamos ciertas tecnologías e intentamos inspirarlos para que sigan nuestros pasos. Ellos serán los encargados de resolver problemas que nosotros ni siquiera podemos imaginar hoy en día", reflexiona Oliver Toogood.
Pero James Dyson siempre va un paso más allá, y por eso fundó el DIET, la gran cantera de Dyson. Tras un exhaustivo proceso de selección, cada año acceden entre 35 y 45 alumnos para obtener un título universitario y entrar a trabajar en Dyson, recibiendo una remuneración desde el primer día. Entre las instalaciones más sorprendentes del campus están los 'pods', unos edificios con forma de cubo en los que se alojan los estudiantes de primer año.
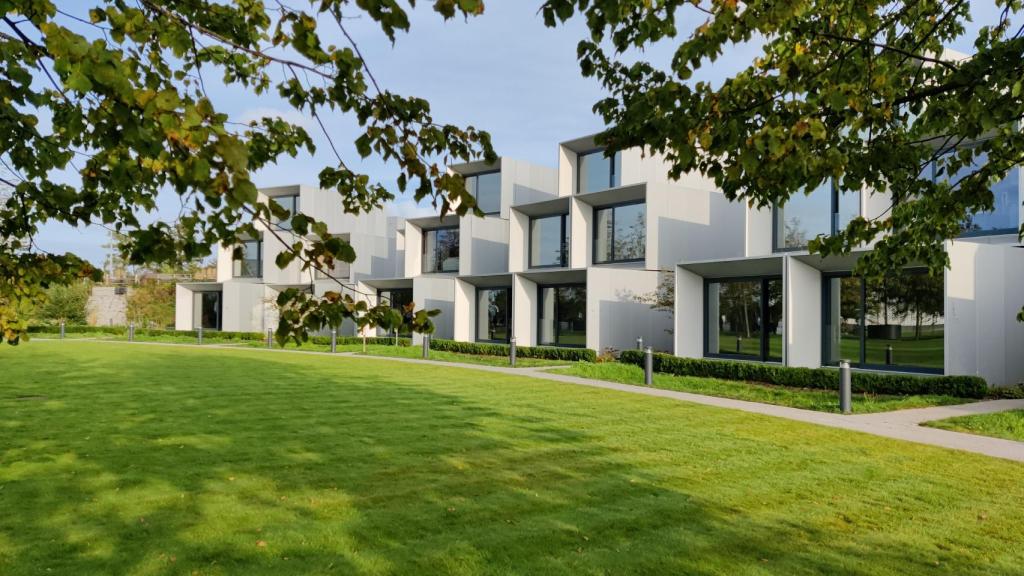
Los 'pods' donde viven los estudiantes de primer año del DIET Omicrono
"Nos dedicamos a cuestiones académicas dos días a la semana, y los otros tres estoy trabajando en distintas rotaciones, así que también participo en temas de I+D", relata ilusionada Alex, una alumna de 21 años que cursa el último año del programa académico del DIET. "Me quedan cuatro meses y luego empezaré a trabajar en mi proyecto de último año, relacionado con sostenibilidad y contaminación".
Para ella, lo más destacado de su paso por el DIET es "poder ver de manera directa cómo trabaja una compañía tecnológica, aunque esta es una empresa bastante peculiar. Vemos todo lo relacionado con un producto desde el principio hasta el final, incluidas las líneas de producción. En una universidad normal como mucho ves cómo se fabrica un prototipo", asegura entre risas. Quién sabe, quizá ella o alguno de sus compañeros sea el próximo James Dyson, alguien llamado a revolucionar toda una industria desde Malmesbury, entre verdes prados y construcciones futuristas.