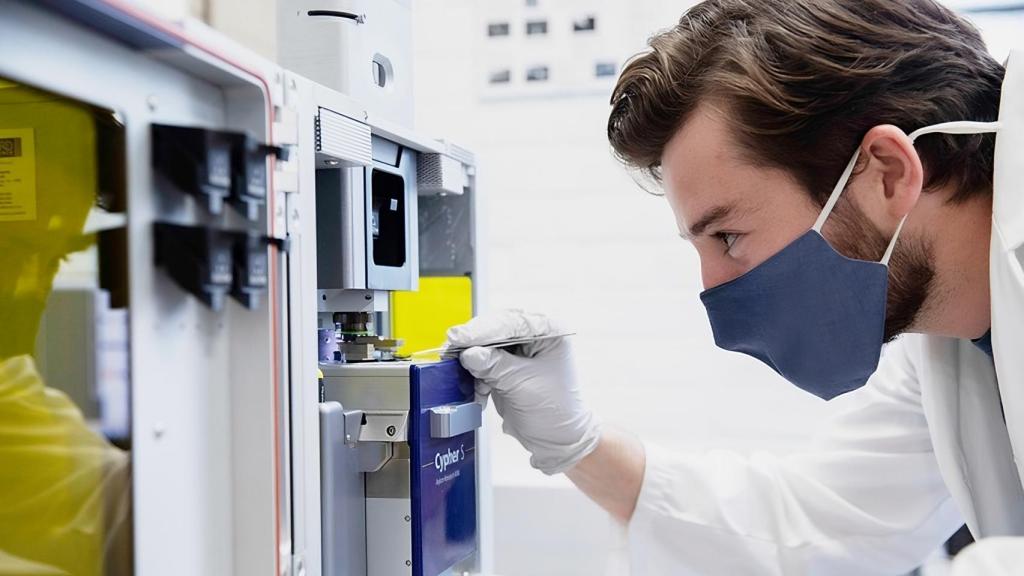
Peter Serles, autor principal de la investigación sobre el nuevo material Omicrono
Cinco veces más resistente que el titanio y tan ligero como el 'poliespán': el novedoso material que cambiará los aviones
El aprendizaje automático ha contribuido decisivamente al desarrollo de este nuevo material basado en carbono y con una novedosa geometría.
Más información: El material que revolucionará los aviones y la exploración espacial: aleaciones de titanio más resistentes y flexibles
Los aviones y los cohetes espaciales son obras maestras de la ingeniería, en constante evolución tecnológica tanto por su diseño como por el desarrollo de piezas clave como los motores. Aviones con alas gigantes y cohetes con reactores nucleares permitirán abaratar los viajes y llegar más lejos que nunca, pero un elemento fundamental en esta ecuación son los materiales con los que se construirá el fuselaje y otros componentes de estos prodigios de la aeronáutica, también en España.
En los últimos años, algunas de las investigaciones más prometedoras del sector se han centrado en los metamateriales y su arquitectura a nivel nanométrico, con resultados sorprendentes en la mejora de sus propiedades estructurales. Recientemente, investigadores de la Facultad de Ciencias Aplicadas e Ingeniería de la Universidad de Toronto han desarrollado un nuevo nanomaterial que aúna una resistencia similar a la del acero al carbono y la ligereza de la espuma de poliestireno, lo que abre enormes oportunidades para su uso tanto en aviones como en la industria aeroespacial.
"Los materiales nanoarquitectónicos combinan formas de alto rendimiento, como hacer un puente de triángulos, en tamaños a nanoescala, lo que aprovecha el efecto 'cuanto más pequeño, más fuerte', para lograr algunas de las relaciones resistencia-peso y rigidez-peso más altas de cualquier material", explica Peter Serles, autor principal del artículo publicado en la revista Advanced Materials, en un comunicado de prensa.
Aprendizaje automático
El potencial de los metamateriales, y más concretamente de los que se forman con estructuras nanométricas, es descomunal. Sin embargo, para que las investigaciones lleguen a buen puerto deben superar numerosos desafíos. El reto principal tiene que ver con el diseño de su geometría, que a veces provoca distribuciones deficientes de la tensión, lo que en último término conlleva su rotura.
Para fabricar estos materiales nanoarquitectónicos se utilizan unos diminutos bloques de construcción idénticos entre sí que se organizan en diseños repetitivos. Para hacerse una idea de lo pequeño que es cada bloque, cien de sus unidades, en este caso compuestas por carbono, tendrían el grosor de un cabello humano.
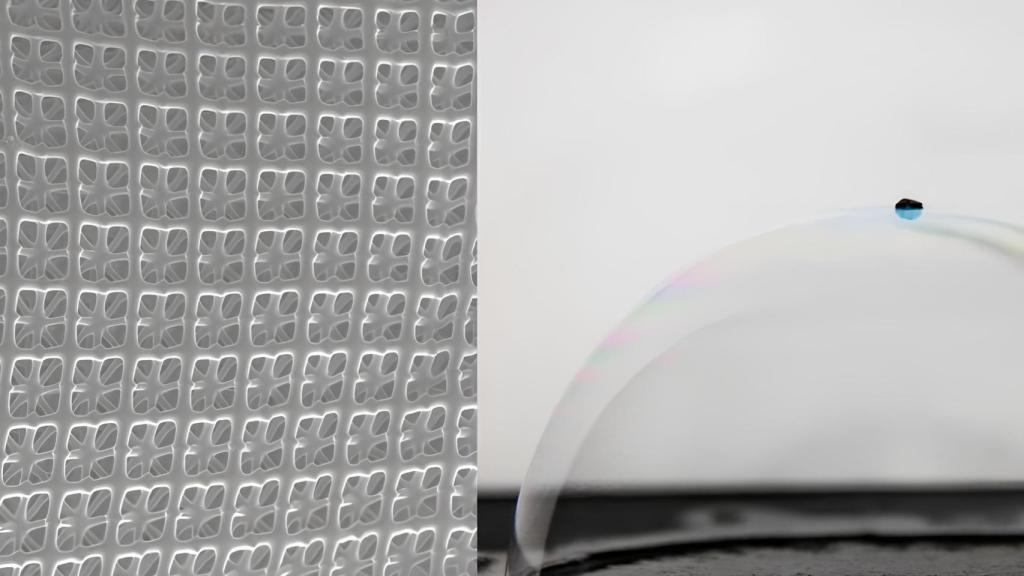
A la izq., la geometría del material, a la dcha., el material resultante flotando en una burbuja. Omicrono
La clave está en cómo se distribuyen estos bloques en complejas estructuras tridimensionales, conocidas como nanoláminas. Para conseguir un diseño óptimo, el equipo de Serles recurrió al conocimiento y la experiencia de los integrantes del Instituto Avanzado de Ciencia y Tecnología de Corea (KAIST). Con su ayuda, utilizó un sofisticado algoritmo de aprendizaje automático capaz de predecir las mejores geometrías posibles para mejorar la distribución de tensiones y la relación resistencia-peso del nuevo material.
"Es la primera vez que se aplica el aprendizaje automático para optimizar materiales con arquitectura nanométrica, y nos sorprendieron las mejoras", sostiene Serles. "No se limitó a replicar geometrías exitosas a partir de los datos de entrenamiento, sino que aprendió de los cambios en las formas que funcionaban y de los que no, lo que le permitió predecir geometrías de celosía completamente nuevas".
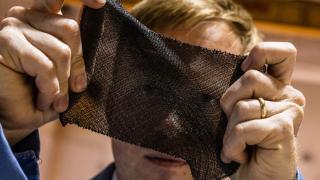
Omicrono
Otra de las ventajas del sistema utilizado por los técnicos del KAIST es la reducción de la cantidad de datos necesarios para el aprendizaje automático, habitualmente muy elevada. "El algoritmo de optimización bayesiana multiobjetivo sólo necesitaba 400 puntos de datos, mientras que otros algoritmos pueden necesitar 20.000 o más", recuerda Serles, por lo que su equipo pudo trabajar con un conjunto de datos mucho más pequeño pero de gran calidad.
Una vez obtenidos esos resultados, la investigación se trasladó al Centro de Investigación y Aplicación de Tecnologías Fluídicas (CRAFT), en Canadá. Allí los ingenieros utilizaron una impresora 3D de polimerización de dos fotones, diseñada específicamente para la impresión 3D de estructuras a escala micro y nanométrica, que les permitió crear los prototipos necesarios para validar los resultados.
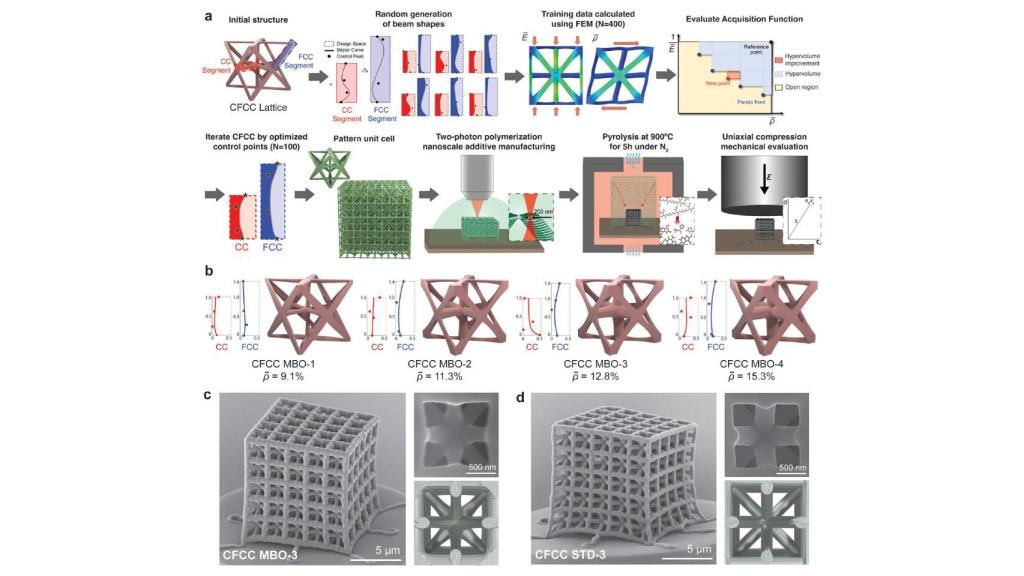
Diagramas de la investigación del nuevo nanomaterial Omicrono
Las nanoláminas resultantes, construidas con 18,75 millones de celdas reticulares con dimensiones nanométricas, sorprendieron por sus propiedades mejoradas: duplicaron la resistencia de diseños previos y fueron capaces de soportar una tensión de 2,03 megapascales por cada metro cúbico por kilogramo de su densidad, cinco veces más que el titanio. El material resultante es tan ligero que puede mantenerse sobre una burbuja de aire sin romperla.
Potencial en los aviones
De momento, las piezas obtenidas con este revolucionario material son demasiado pequeñas, de apenas unos centímentros, pero los investigadores ya buscan la manera de escalar su fabricación y permitir así la producción de componentes a macroescala que sean rentables.
Tampoco se conforman con los resultados, ya que seguirán explorando nuevos diseños para que los materiales resultantes tengan una densidad aún menor sin perder sus cualidades de resistencia y rigidez. Las miras están puestas en el futuro cercano y en las posibilidades que se abren para una auténtica revolución tanto en el sector aeronáutico como en el aeroespacial.
"Esperamos que estos nuevos diseños de materiales acaben dando lugar a componentes ultraligeros en aviones, helicópteros y naves espaciales, que puedan reducir la demanda de combustible durante el vuelo manteniendo la seguridad y el rendimiento", explica Tobin Filleter, el impulsor de la investigación. "En última instancia, esto puede ayudar a reducir la elevada huella de carbono que supone volar".
De hecho, según los cálculos del equipo, si se sustituyeran los componentes de titanio de un avión por este nuevo material, se ahorrarían 80 litros de combustible al año por cada kilogramo de material sustituido. Esto reduciría enormemente el consumo de combustible necesario para volar y, por tanto, las emisiones de gases de efecto invernadero.
"Ha sido un proyecto polifacético que ha reunido diversos elementos de la ciencia de los materiales, el aprendizaje automático, la química y la mecánica para ayudarnos a entender cómo mejorar y aplicar esta tecnología", resume el propio Serles.