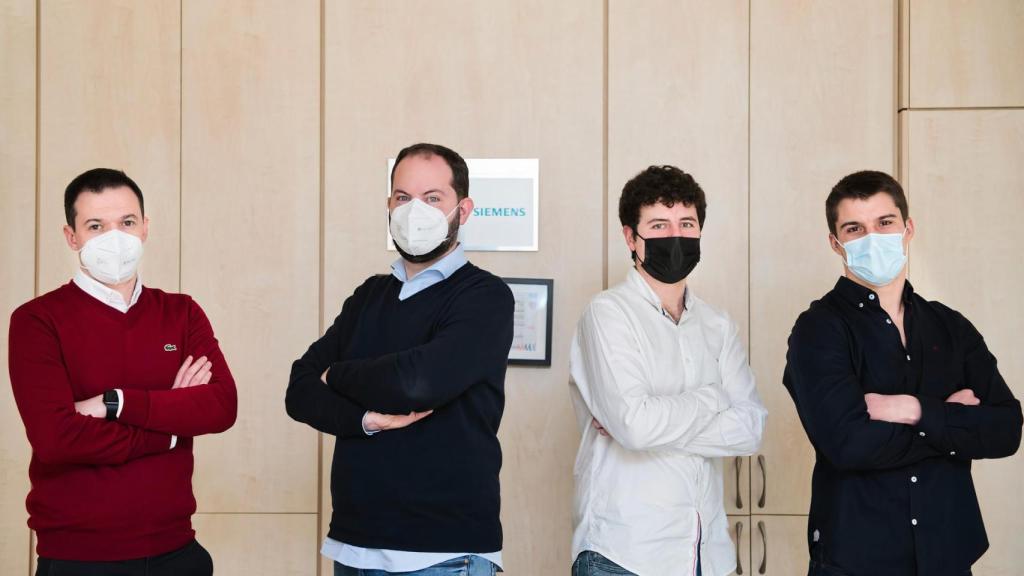
El equipo de Tecdesoft
Tecdesoft: Obteniendo valor tratando los datos industriales de Galicia
Análisis del proceso de recogida de datos en la industria, y los beneficios de una correcta utilización de los mismos. ¿Están las fábricas gallegas concienciadas sobre este tema?
19 marzo, 2021 06:00En estas fechas en las que el concepto de industria 4.0 ya no es ajeno a nadie, sorprende ver cómo la adopción de la aplicación de la analítica de datos tiene tan poca penetración en nuestro parque industrial. Existe una carrera por aplicar IoT, implementada sin un criterio industrial en muchos casos, en búsqueda y captura del dato. Sin embargo, existe muy poca concienciación de cómo utilizar este dato que es precisamente donde reside el valor.
Obtención de los datos
El primer paso, y fundamental, es recoger correctamente los datos generados en la fábrica.
Sin unos datos veraces y útiles, su posterior análisis carecería de sentido. Por ello, hoy en día se antoja fundamental automatizar la captura de datos en planta.
Esta automatización constituye uno de los pasos fundamentales en el proceso de digitalización de la fábrica, ya que permite seguir y controlar de forma precisa cada uno de sus procesos.
Para ello, una vez se tienen los datos a nivel de línea de producción, es importante centralizarse en un sistema de adquisición de datos, ya que normalmente las líneas de fabricación son “islas” aisladas que no saben nada de las demás.
Precisamente en la relación de la información de estas “islas” es dónde está la complejidad de tener un dato de buena calidad. No es el único factor que influye para ello, pero sí que hay que tenerlo muy en cuenta.
Un ejemplo de esto puede ser el proceso de producción de un yogur. Es fundamental tener la trazabilidad unitaria de todos los elementos que intervienen en el mismo. Esto consiste en conocer todas las variables que han formado parte del proceso, con todos los valores que han tenido hasta lograr conformar (de dónde vienen los materiales, que los transportó, qué temperatura ambiente había durante el proceso, …)
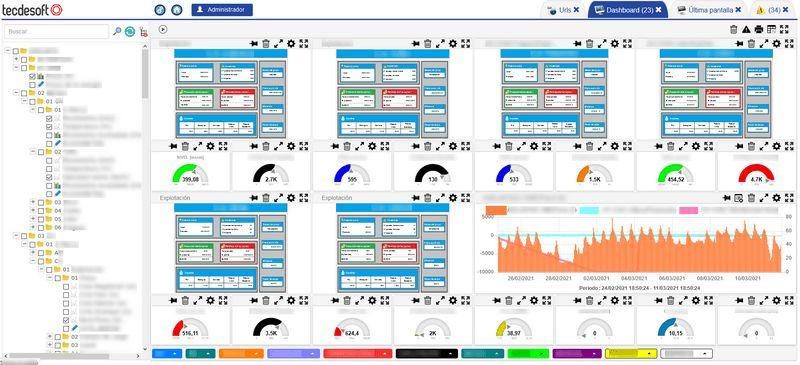
El "Dashboard" de Carmen
El software CARMEN (Collector of Smart Metrics), desarrollado por Tecdesoft, es un sistema de adquisición de datos en entornos distribuidos, que además de adquirir datos en tiempo real, realiza otras tareas típicas de la supervisión como son la generación de incidentes y la monitorización.
Análisis de los datos
Una vez tenemos nuestros datos centralizados y normalizados, podemos empezar a hablar ya sobre su tratamiento.
Hablando un poco sobre nuestra experiencia personal, el proceso de normalizado es el que lleva más esfuerzo en los proyectos de analítica que hemos afrontado, porque nadie se había parado nunca a pensar en su importancia.
Si se lo hubiesen planteado en el momento de hacer el control industrial, tendría un impacto muy reducido y los datos almacenados tendrían mucho más valor.
Este es claramente un valor diferencial de Tecdesoft, plantear el control industrial preparado para que cuando el cliente quiera, pueda extraer valor de los datos almacenados.
Centrándonos un poco más en la teoría, el proceso habitual en la analítica parte de:
- Una pregunta de negocio que se quiere responder. Por ejemplo, ¿Cuántas piezas con defectos se están fabricando por lote?
- Con esta pregunta, se busca con qué datos se podría responder.
- Una vez seleccionados, se genera una ETL, que se encarga de recopilar todos estos datos en distintas fuentes heterogéneas y dejarlas en único sitio para que el analista pueda responder.
- Los analistas estudian los sets de datos, generando modelos de IA en caso de ser necesarios, para dar respuesta a la pregunta y hacer predicciones a futuro.
Llegados a este punto, muchos os preguntaréis qué es una ETL. ETL viene del inglés y significa “Extract, Transform and Load”. Es el proceso mediante el cual se extraen datos de las fuentes de negocio, se transforman preparándonos para el análisis y por último se cargan en el almacén de datos para que los analíticos puedan extraer valor de negocio de los datos.
Dependiendo de la pregunta a la que se quiera dar respuesta, nos interesará aplicar un tipo de analítica u otra en nuestra fábrica. Desde un punto de vista funcional, existen 4 formas de catalogar la analítica aplicada a la industria.

El software de Tecdesoft
Analítica descriptiva
Es la forma más básica de analítica. Su función consiste en describir el proceso y los sistemas que lo sustentan. Responde al ¿Qué está pasando?
Aunque no lo parezca, en esta forma de analítica se puede profundizar mucho obteniendo un beneficio inmediato. Por ejemplo, contar con una plataforma de monitorización, como CARMEN, que permita ver de una forma centralizada todos los sensores (en tiempo real) de las distintas plantas, me permite contrastar y analizar datos de distintas líneas, visualizar KPIs, tener el histórico de la sensórica de producción para aprender de lo que ha pasado, etc.
Una selección correcta de los datos a visualizar y una eficiente organización de los mismos es fundamental para poder obtener información útil a primera vista.
Analítica de diagnóstico
Responde a la pregunta ¿por qué está pasando?
Normalmente se utiliza para responder al ¿por qué ha pasado este problema? y poder establecer medidas para que no vuelva a suceder (en caso de ser necesario).
Para poder responder a la pregunta, se debe dotar al personal de planta de las herramientas apropiadas para realizar el diagnóstico lo antes posible. Si puedo saber por qué se produce una parada, puedo restablecer el proceso mucho más rápidamente, minimizando el lucro cesante.
Las herramientas de gestión de alarmas y eventos que siguen el estándar ISA 18.2 son un ejemplo de ayuda rápida a los operadores, que además, consiguen un mayor protagonismo al relacionarlos con las herramientas de la analítica descriptiva.
Analítica predictiva
Responde a la pregunta ¿Qué es lo más probable que pueda pasar?
Con este tipo de analítica puedes predecir, por ejemplo, los valores de los sensores y saber si el valor actual está en el rango adecuado (aunque no suponga una alarma de proceso), podrías determinar con una muy alta probabilidad el tiempo que falta hasta el siguiente fallo en una máquina, para saber cuándo hacer el mantenimiento o la probabilidad de que un producto se salga de los parámetros de calidad definidos.
En este punto ganas un conocimiento profundo del proceso, viendo detalles que antes pasaban inadvertidos.
Analítica prescriptiva
Responde a la pregunta: ¿Qué necesito hacer?
Es el tipo de analítica más avanzada y se basa en conocer y entender lo que ha sucedido, por qué ha sucedido y lo que podría suceder para ayudar al personal de planta a determinar las mejores acciones a tomar.
En otras palabras, te permitiría determinar las condiciones en las que un producto se fabrica con la mejor calidad, el menor coste o el requisito que le queramos aplicar.
En este tipo de analítica se aplican algoritmos de Inteligencia Artificial y Machine Learning que ayudan a mejorar constantemente y a fabricar con cero defectos
Como se puede ver, la analítica tiene beneficios desde el primer minuto, siempre y cuando se haga con con criterio y conociendo cómo funciona el proceso en la fábrica.