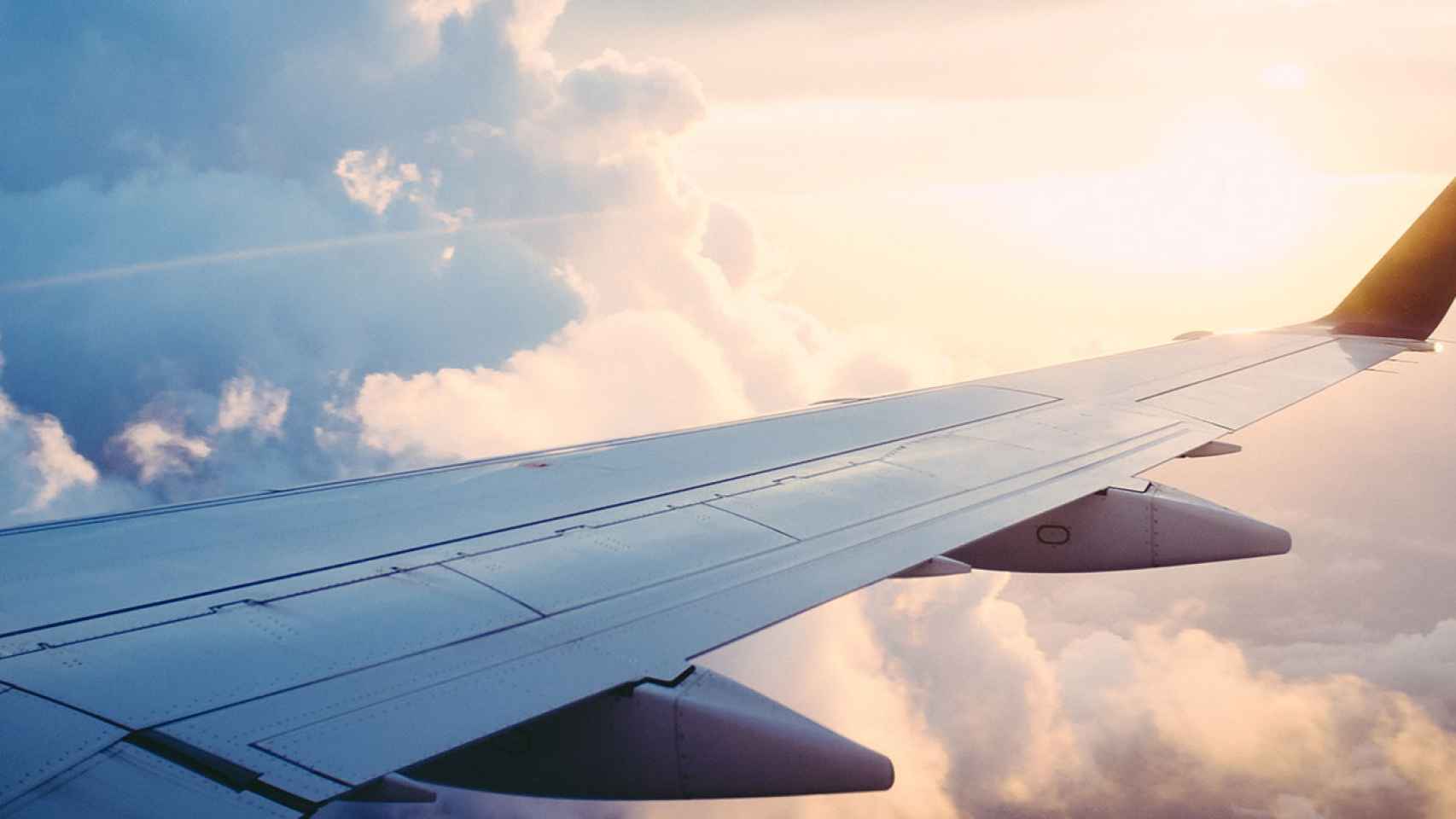
Sensores impresos en 3D que detectan fallos estructurales en materiales
Investigación
Sensores impresos en 3D que detectan fallos estructurales en materiales
Investigadores del grupo de Ciencia e Ingeniería de Materiales de la URJC han conseguido convertir (con nanotecnología e impresión 3D) la resina en un sensor natural que detecta fallos en estructuras de las piezas de aviones, torres eléctricas, camiones....rn
9 julio, 2020 12:04Controlar la vida útil y el mantenimiento de cualquier estructura es vital para prevenir fallos o accidentes. Por eso es importante monitorizar la salud estructural de un material (lo que los ingenieros llaman SHM, Structural Health Monitoring) para detectar posibles cambios o deformaciones que puedan afectar a sus propiedades.
El equipo de investigación del grupo de Ciencia e Ingeniería de Materiales de la Universidad Rey Juan Carlos (URJC) ha diseñado con impresión 3D unas piezas de resina capaces de monitorizar un daño en la estructura. La tecnología de impresión 3D les permite crear materiales compuestos que confieren conductividad eléctrica a la matriz polimérica y permiten así auto detectar alguna variación de sus propiedades.
Para ello, han utilizado resinas reforzadas con nanotubos de carbono (denominados CNT), logrando que la resistencia eléctrica final del material varíe si se produce alguna deformación o se detecta la presencia de un daño. “La monitorización de esta magnitud nos permite conocer, de manera remota y autónoma, el estado estructural de la pieza. Esto se conoce como monitorización de la salud estructural”, explica Alberto Jiménez, investigador grupo de Ciencia e Ingeniería de Materiales y coautor del estudio publicado recientemente en la revista científica Polymers.
Tal como explican desde la URJC, la utilización de tecnología de impresión requiere de luz UV para curar la pieza de resina, es decir, para conseguir que el material empleado se convierta en el polímero deseado. Para llevar a cabo este estudio se ha empleado una impresora 3D DLP (digital light processing) en la cual, mediante la utilización de resinas fotocurables, se han ido creando piezas capa a capa. “Cada una de estas capas es expuesta a una irradiación de luz ultravioleta que activa el curado de la pieza hasta un grado tal que permite curar otra capa a continuación para que quede completamente integrada con la anterior, por lo que el grado de curado alcanzado en cada capa debe ser correctamente controlada”, explica Alberto Jimenez.
En los ensayos realizados con las piezas fabricadas con este sistema se ha demostrado que esa capacidad de monitorizar su salud estructural otorga una mayor seguridad a la hora de emplear estos materiales en componentes cuyo fallo imprevisto supondría un grave problema e incluso un accidente fatal como es el caso de los sectores del transporte y la energía.