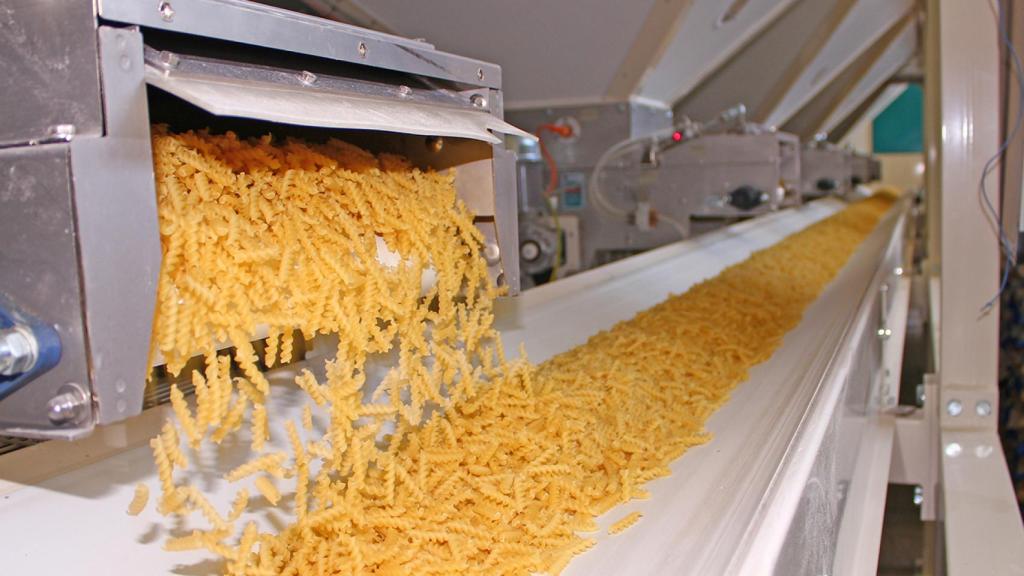
Generar vapor con partículas cerámicas para fabricar la pasta italiana Barilla
Generar vapor con partículas cerámicas para fabricar la pasta italiana Barilla
La española Sugimat diseñará y fabricará el generador de vapor de una innovadora central termosolar para producir pasta Barilla en su planta de Foggia
17 noviembre, 2020 07:00Reducir la huella de CO2 de la producción de pasta. Este es el reto al que se enfrenta el fabricante Barilla en su planta de Foggia (Italia), que apuesta por la energía termosolar para producir su famosa pasta y mitigar el consumo de combustibles fósiles. El sistema que se ha diseñador será capaz de hacer funcionar la planta 24 horas al día, siete días a la semana con fuentes renovables.
Se trata del proyecto de investigación europeo HiFlex, en el que participan 11 empresas industriales e institutos de investigación de siete países. Entre ellos, la española Sugimat, encargada de diseñar y fabricar el generador de vapor y el condensador de este innovador sistema termosolar.
El punto de partida del piloto es una planta de energía de torre solar con alrededor de 500 espejos móviles, llamados heliostatos, que enfocan los rayos solares en la parte superior de la torre, donde un receptor solar especial absorbe la radiación solar concentrada.
En su interior está uno de los ingredientes secretos de este proyecto: pequeñas partículas de cerámica de un milímetro, que fluyen a través del receptor. ¿Por qué un elemento sólido y no un fluido como es habitual en las centrales termosolares? Alex Mas, director de Desarrollo de Negocio de Sugimat, explica que en estas centrales de primera y segunda generación se empleaba como fluido bien un tipo de aceite térmico (pueden alcanzar los 400 grados), bien sales diluidas (600 grados) para generar el vapor que se necesitaba en este sistema.
Sin embargo, en HiFlex están diseñando la que será una tercera generación de plantas termosolares capaz de alcanzar y conservar mayores temperaturas. “A mayor temperatura del fluido primario, mayor rendimiento del ciclo agua-vapor”, destaca Mas a INNOVADORES.
La mayor parte de los fluidos no aguanta más de 400-600 grados, por lo que este proyecto apuesta por calentar partículas cerámicas que pueden “alcanzar 1.000 grados sin degradarse durante un mayor tiempo”, incluso, puede mantenerse la temperatura por la noche. Cuanto más calor, más calidad de vapor, y cuanta más calidad de vapor, más rendimiento de la turbina.
Cuando se quiera disponer de esa energía, hay que trasladar las partículas a un generador de vapor, pieza que va a desarrollar la española Sugimat, para intercambiar el calor de las partículas con agua y así crear el vapor con el que se generará electricidad. En el caso de la fábrica de Barilla, lo que se genera es vapor de proceso para la planta de pasta de italiana, apunta Mas.
Una vez extraído el calor de las partículas estas se almacenan a 300 grados en otro tanque a la espera de necesitar nuevamente partículas para volver a iniciar el proceso. “Se trata de un circuito cerrado” en el que si se enfría el material “ no hay mayores consecuencias”, en cambio en los fluidos de primera y segunda generación ““a bajas temperaturas se solidificaría”, subraya el responsable de Sugimat.
El “desafío”, afirma Mas, es tanto transportar las partículas a 1.000 grados como el diseño y la fabricación del generador de vapor. Si se tratara de un generador tradicional sería “un fluido que circularía a través de unos tubos sumergidos en agua para producir vapor”, pero, en este caso, la complejidad estriba en que “no se trata de un fluido al uso, sino de un material sólido [las partículas cerámicas] que hay que conseguir que fluya”.
Una de las ventajas de este sistema es la flexibilidad que puede aportar, al ser capaz de compensar las fluctuaciones y almacenar la energía que no se consume inmediatamente como partículas calientes y ponerla a disposición de la fábrica cuando sea necesario. De este modo se puede lograr una potencia máxima de 2,5 megavatios térmicos y, además, el sistema contará con una capacidad de almacenamiento de 20 megavatios/hora térmica.
HiFlex
El equipo del proyecto HiFlex también tiene una solución para los días nublados: “Alternativamente, podemos calentar las partículas con viento renovable, solar o biogás”, explica Miriam Ebert del Instituto de Investigación Solar del DLR, otro de los miembros de este consorcio empresarial para este proyecto europeo.