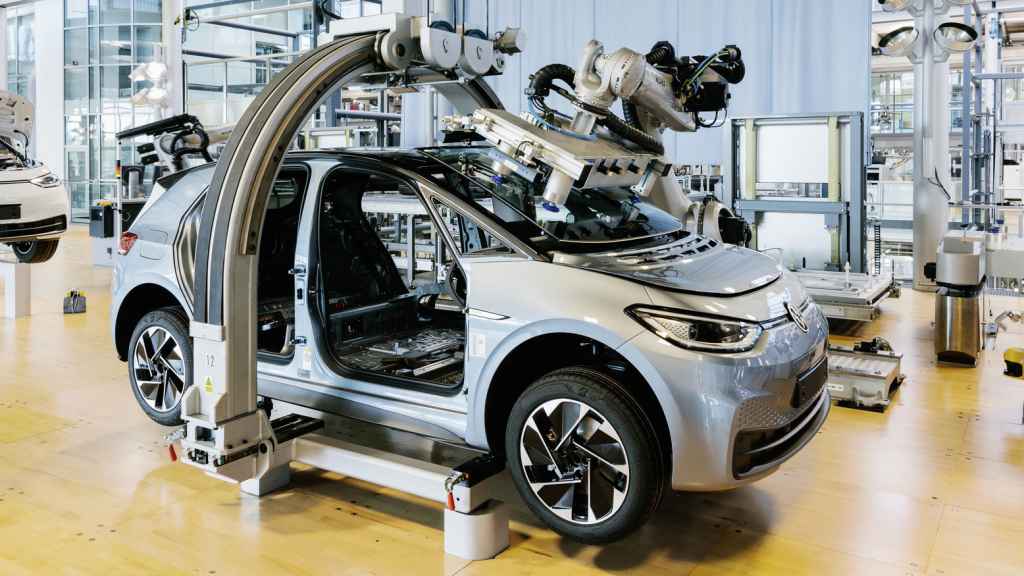
El coche eléctrico Volkswagen ID.3 durante su fabricación.
Visitamos el corazón del coche eléctrico en Europa: así lucha Volkswagen con Tesla por el liderazgo mundial
- Las fábricas de Dresde y Zwickau, en Alemania, son dos plantas 'clave' para comprender la estrategia del Grupo Volkswagen en la transformación hacia el coche eléctrico.
- Coches nuevos: precios y ofertas | Coches híbridos | Coches eléctricos | Coches de segunda mano
Noticias relacionadas
Europa cada vez tiene un papel de mayor peso en la fabricación de vehículos eléctricos, un hecho que hemos vivido en primera persona de la mano de Volkswagen en sus plantas de Dresde y Zwickau (Alemania).
Si bien la fabricación de coches puede parecer algo complicado de entender, con nuestra experiencia en las fábricas sajonas vamos a intentar desmentir esa idea. El Grupo Volkswagen en los últimos años se ha puesto las pilas en términos de estrategia eléctrica, algo que se ve reflejado en los resultados obtenidos.
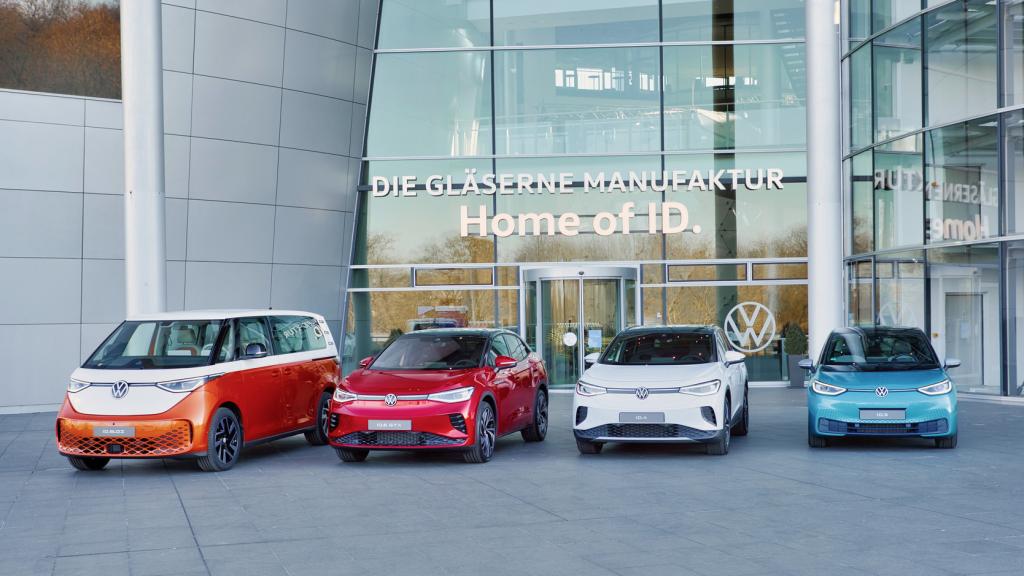
La gama ID de Volkswagen cuenta con una amplia oferta de carrocerías.
En la carrera por el coche eléctrico, Tesla será el líder claro de 2022 con cerca de 1,2 millones de unidades producidas, según nuestras estimaciones. Tras Tesla, le siguen BYD y SAIC Motor con cerca de 800.000 y 650.000 unidades previstas respectivamente.
Y la cuarta posición será para el Grupo Volkswagen, que este año ensamblará aproximadamente 500.000 coches eléctricos (en los tres primeros trimestres ha matriculado 360.000 coches eléctricos).
Recordamos en este sentido que el consorcio alemán cuenta con un total de 120 plantas de producción en el mundo. Y de todas ellas, ya hay cerca de una decena de fábricas donde se ensamblan vehículos de cero emisiones. Son, entre otras, Foshan (China), Anting (China), Changchun (China), Neckarsulm (Alemania), Zwickau (Alemania), Bruselas (Bélgica), Dresde (Alemania) y Mladá Boleslav (República Checa).
Y a todas ellas hay que sumar, en cuestión de solo unos años, las plantas españolas de Martorell (de Seat y Cupra en Barcelona) y Landaben (de Volkswagen en Navarra). Dos fábricas que sumarían casi cerca de 800.000 eléctricos cuando estén a pleno rendimiento en la fabricación de eléctricos a finales de la década.
Pues bien, desde EL ESPAÑOL hemos tenido la oportunidad de conocer dos del estado de Sajonia: Dresde y Zwickau. Estas plantas, por tanto, son clave en la carrera de Volkswagen por el coche eléctrico. Cada una de ellas es un concepto completamente distinto, una manera única de vivir el momento de producción de un coche, así como sus dimensiones, empleados y unidades fabricadas. Desde nuestra experiencia os contaremos todo lo que hemos aprendido sobre este tipo de lugares que por fuera pueden parecer tan grises.
Dresde: donde los sueños se hacen realidad
También conocida como la 'fábrica de cristal' por su diseño vanguardista de superficies acristaladas, se edificó entre 1999 y 2001. Antiguamente respaldaba la idea de "Centro de Movilidad del Futuro", sin embargo, ahora sirve como "Hogar de la Familia ID" (la gama de vehículos eléctricos de Volkswagen).
Esta pequeña fábrica comenzó su andadura en 2001 con la producción del Volkswagen Phaeton y posteriormente se encargó también del Bentley Flying Spur y el Volkswagen e-Golf. En enero de 2021 iniciaron una nueva etapa, una llena de retos y cambios vertiginosos, la movilidad 100% eléctrica.
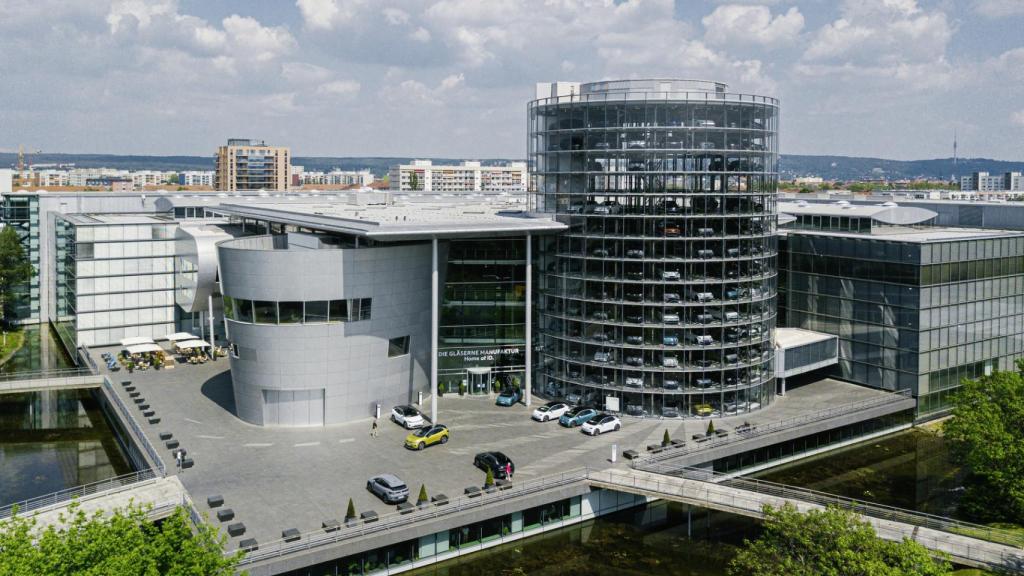
La Fábrica de Dresde se edificó entre 1999 y 2001.
El protagonista de este nuevo capítulo fue el primer modelo completamente eléctrico de la firma alemana: el Volkswagen ID.3. Con la confección de este coche compacto han revolucionado la manera de entender los procesos de producción, acercando así a cualquier persona interesada a conocer cómo se monta un vehículo cero emisiones.
Al entrar en este espacio todo tiene un gusto exquisito y moderno, con varios pisos de altura y coches expuestos como si de un escaparate se tratase. Todo esto ya señala que no es una fábrica al uso, sino una nueva experiencia única para visitantes, invitados y clientes.
Tuvimos la enorme suerte de poder hacer un recorrido para conocer los entresijos de este lugar tan peculiar, comenzando por la sala donde se hace la entrega de los vehículos a sus dueños.
Aquí se proyecta un vídeo del Volkswagen ID.3 entre pantallas de grandes dimensiones, acompañado de una bienvenida con un tentempié, una explicación con todo lujo de detalles sobre el vehículo e incluso una visita guiada por las instalaciones.
Tras esta experiencia, subimos a las líneas de montaje, donde curiosamente los suelos son de madera canadiense y le dan un aspecto mucho más acogedor. Al tratarse de una fábrica pequeña, solo tiene dos líneas de montaje y 340 empleados, cuyo récord de entregas fue en 2021 alcanzando las 4.320 unidades.
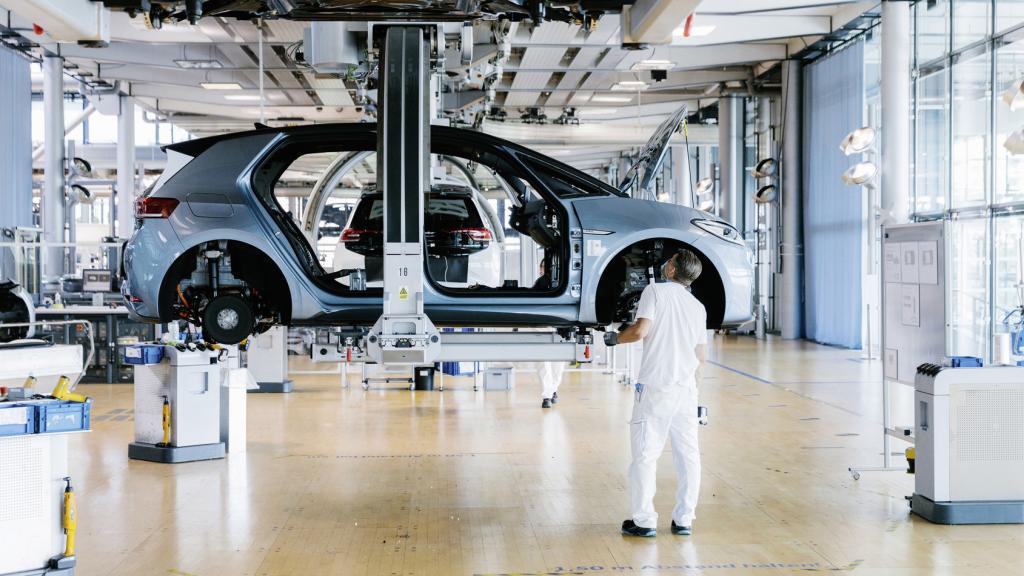
En el interior de la planta destacan los suelos de madera canadiense.
Una de las actividades más interesantes que realizamos durante la visita fue la de ser partícipes en la producción del Volkswagen ID.3. De esta manera, y con la ayuda de un profesional colocamos los embellecedores del techo, la pieza que despresuriza el interior del coche o el remate final de instalar el logotipo de la marca en el frontal (entre otros).
La fábrica de Dresde es una auténtica área de experiencia, donde no solo se producen coches y se realizan visitas guiadas, sino que sirve como una plataforma de comunicación para diversos eventos en función del tipo de público (general, de empresa o políticos).
Zwickau: metamorfosis hacia la era eléctrica
La planta de Zwickau también se encuentra en el estado de Sajonia y es la fábrica principal de la zona, ya que cuenta con más de 11.000 empleados y tiene una producción de 300.000 unidades al año. Aquí se fabrican seis modelos de tres de las marcas del grupo.
Concretamente son el Volkswagen ID.3, Volkswagen ID.4 y el Volkswagen ID.5, así como el Audi Q4 e-tron, Audi Q4 Sportback e-tron y el Cupra Born. A diferencia de la planta de Dresde, esta cuenta con un aspecto mucho más industrial y es el núcleo de la estrategia de descarbonización denominada como 'Way to Zero' del gigante alemán.
En 2019 se empezó una transformación del 85% de las instalaciones para conseguir una planta totalmente capacitada para la producción de vehículos eléctricos, con una inversión de 1,2 billones de euros. Toda esta gran revolución tiene (en parte) su causa en el objetivo del año 2050: ser neutral en emisiones de CO2 en todas sus actividades.
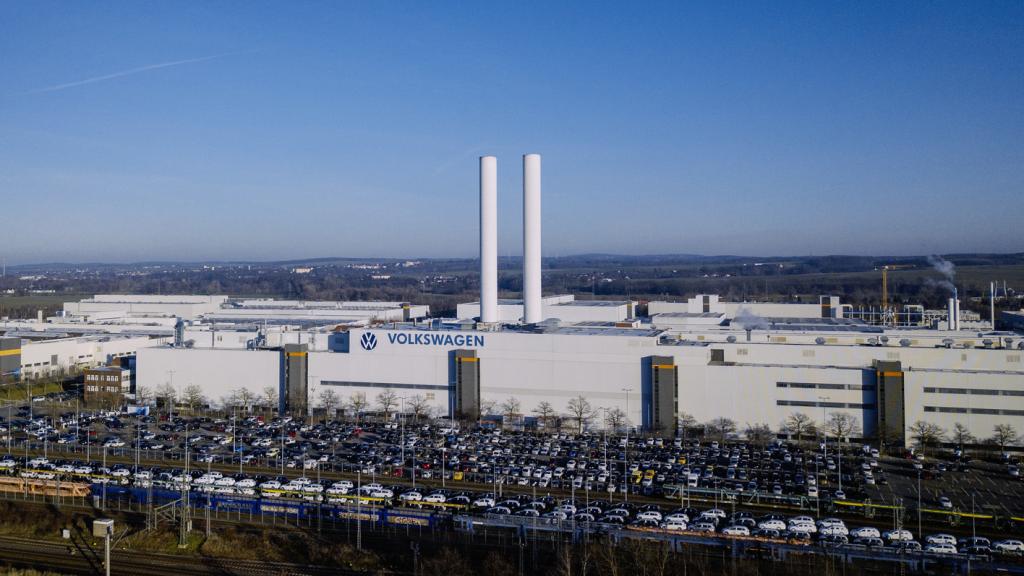
La Fábrica de Zwickau es la principal planta del Estado de Sajonia.
Además, para 2030 quieren lograr reducir un 45% las emisiones nocivas por cada vehículo, y esto incluye tanto las cadenas de suministro como la propia producción.
Este gran cambio de la planta de Zwickau ha traído consigo un grado de automatización mayor (90%) y más herramientas digitales para facilitar los procesos. En este sentido, pudimos presenciar el trabajo de los robots inteligentes 'Industria 4.0' en la propia fábrica, los cuales cuentan con una precisión que deja a cualquiera con la boca abierta. Podríamos decir que cada milímetro importa.
Una de las preguntas más recurrentes al ver que muchos pasos son realizados por máquinas y no por humanos es la siguiente: ¿esto hace que se pierdan puestos de trabajo? Los responsables de la planta de Zwickau respondieron que no, ya que para que los robots funcionen debe estar una persona supervisando que todo salga correctamente.
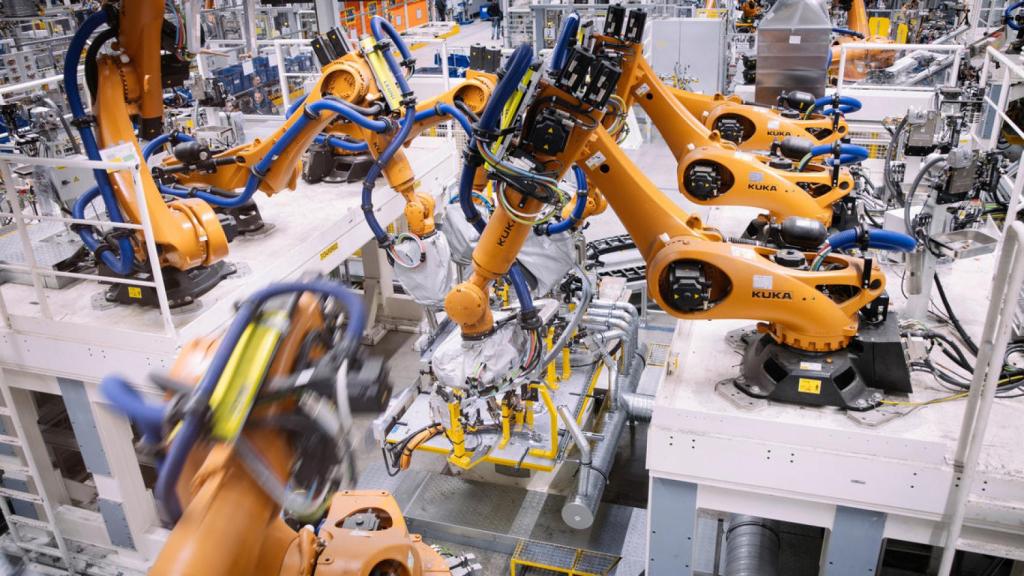
El nivel de automatización alcanza el 90% de los procesos de producción.
Asimismo, con esta conversión hacia una planta de vehículos eléctricos se ha pasado de 8.000 a 11.000 empleados, y con la responsabilidad de seguir de cerca los procesos automatizados los trabajadores adquieren un certificado con más reconocimiento.
La última parte de nuestra visita por esta extensa fábrica fue la de conocer el lado más humano, el verdadero motor que hace que todo siga su curso. Con tanto cambio en estos últimos años los empleados reciben diversas formaciones, en función de la complejidad de cada modelo.
Lo más interesante de está área es la originalidad con la que el Grupo Volkswagen ha sabido encajar la enseñanza con el mundo eléctrico. Ejemplo de ello es uno de los centros de entrenamiento: un verdadero 'Scape Room'. Este cuenta con tres salas y se deben ir superando las pruebas de cada una de ellas para seguir avanzando.
El objetivo principal es aleccionar de una manera más entretenida la importancia del coche eléctrico y su trayectoria a lo largo de la historia. Esta "prueba" se realiza por las mañanas antes de entrar a trabajar y ya lo han hecho dos terceras partes de la plantilla.
Sostenibilidad en todas las fases
Como hemos recalcado antes, para año 2050 el Grupo Volkswagen quiere ser neutro en todas sus actividades al producir sus coches. Esto no solo implica los procesos de fabricación en las plantas como tal, sino que también incumbe a las cadenas de suministro.
Por ello, desde 2020 el transporte de las baterías de los ID.3 e ID.4 se realiza con trenes eléctricos y, para la última parte del trayecto con camiones cero emisiones. Por otro lado, el envío de nuevos vehículos a través de rutas marítimas se lleva a cabo con combustibles elaborados a partir de residuos vegetales.
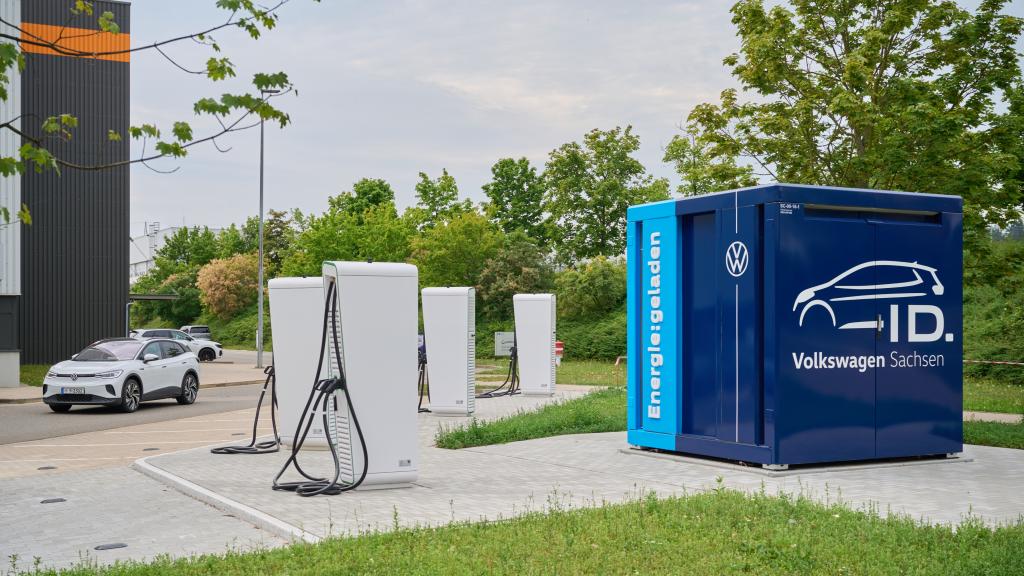
Las baterías tienen una segunda oportunidad como generador de energía para puntos de recarga.
¿Y qué pasará en un futuro con las baterías al final de su vida útil? Los responsables de esta área aseguraron que se reciclará la mayor parte de las materias primas utilizadas, como el litio, el níquel y el cobalto. De hecho, una manera de reutilizar las baterías es transformando su función en puntos de recarga, ya que las mismas se almacenan en contenedores y desde ahí administra su energía.
También te puede interesar...
- Todos los precios y ofertas de los coches nuevos en España
- Precios y ofertas de coches híbridos | Coches híbridos enchufables | Coches eléctricos
- Listado con los principales coches con etiqueta eco
- Coches con etiqueta cero de la Dirección General de Tráfico
- Precios y ofertas de coches de segunda mano
- Todos los coches SUV | Coches SUV medianos | Coches SUV urbanos